Virtuelle Kabineneinrichtung
Virtual Fitcheck heißt das neue Verfahren, das die gängige Praxis revolutionieren soll, Elemente der Kabinenausstattung dem realen Flugzeug anzupassen. Wir befinden uns dabei im Bereich VIP & Executive Jet Solutions der Lufthansa Technik AG in Hamburg, wo ein Team um Oliver Thomaschewski an dieser virtuellen Flugzeugkabine arbeitet. Die Kunden dieses Bereichs haben viel Geld und eine Menge Extrawünsche, wenn es um die Ausstattung ihres Privatflugzeugs geht. „Das kann ein neues oder ein gebrauchtes Flugzeug sein“, sagt Thomaschewski, „aber für uns ist es immer erst einmal ein unbekanntes Wesen mit der Losgröße 1.“ Ein Einzelexemplar also, das sich ziemlich von seinem Vorgänger oder Nachfolger unterscheidet.
Die Wahl der Ausstattung
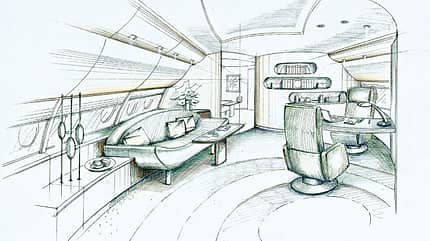
Während der Vertragsverhandlungen werden die Einzelheiten der künftigen Kabinenausstattung festgelegt, die Raumaufteilung, Farben, Materialien und vieles andere mehr. Nicht jeder Wunsch ist realisierbar, nicht einmal für alles Geld der Welt, doch die Experten von LHT bieten Lösungen an, mit denen zum Schluss jede Seite leben kann. Danach wird – in gewissen Grenzen – schon vorproduziert, damit die Installationen zügig erfolgen können, wenn das Flugzeug in Hamburg eintrifft. Theoretisch jedenfalls. In der Praxis indessen ist das nicht ganz einfach.
Wenig Daten vorhanden
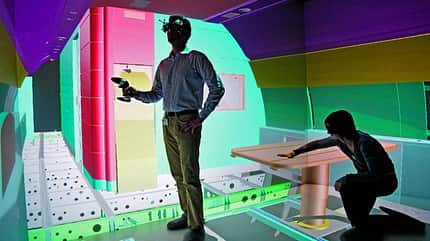
Überraschenderweise kann man nicht einfach in die Dokumentationen der Maschine sehen und sich die erforderlichen Daten herausziehen, denn die Hersteller halten solche Daten wegen der Konkurrenz zurück. Von einer Boeing 737 beispielsweise, einem gern für VIP-Ausstattungen genutzten Muster, existieren nur Papierunterlagen. Das erste Flugzeug, von dem 3-D-Computerdaten existierten, war die Boeing 777!
Deshalb muss jede Maschine, wenn sie in Hamburg eintrifft, erst einmal gründlich vermessen und gecheckt werden, bevor die Ausstattung beginnen kann. Bei den Checks wird unter anderem festgestellt, wo sich Kabel und Leitungen befinden, feste Einbauten und ähnliche Installationen, und oft stellt sich heraus, dass das Flugzeug anders aussieht, als man bei Annahme des Auftrages dachte.
Fertigung der Einbaumöbel und Fitcheck

Dennoch beginnt schon vorab die Fertigung von Einbaumöbeln, allerdings noch ohne Lackierung oder die Verkleidung mit edlen Furnieren. „Bisher bauen wir immer noch auf Übermaß“, erläutert Oliver Thomaschewski, „dann räumen wir alles in die Kabine und sehen zu, dass alles passt. Ein Stück absägen kann man ja immer noch.“
Diese erste Funktionsprüfung wird Fitcheck genannt. Schließlich wird alles wieder ausgeräumt und die Finalisierung beginnt in den Werkstätten. Das kann bis zu drei Monaten dauern, doch genau das war ausschlaggebend für das Forschungsprojekt „Virtual Fitcheck“.
Die Grundidee bestand darin, tatsächlich die Möbel so zu produzieren, dass man auf die umständliche Anpassungsphase und die anschließende Finalisierung verzichten kann. Immerhin steht das Flugzeug in diesen drei Monaten in der Halle herum, so dass der Kunde es nicht nutzen kann, und bei LHT wird ein Hallenplatz belegt, auf den eigentlich schon der nächste Kunde wartet.
Die virtuelle Kabine
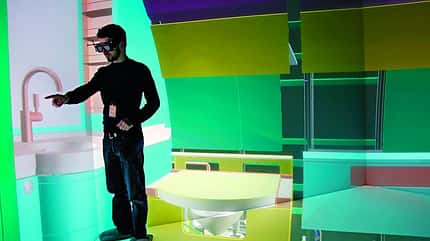
„Um unser Flugzeug als virtuelles Modell darstellen zu können, gingen wir Kooperationen mit fünf Universitäten und Hochschulen ein“, berichtet Thomaschewski, „wobei wir viele Bereiche zusammenführten, die normalerweise nichts miteinander zu tun haben.“ Im Ergebnis der Arbeit entstand eine begehbare Kammer mit Glaswänden, die sogenannte CAVE (Cave Automatic Virtual Environment). Sie ist nur zwölf Quadratmeter groß, aber mit Hilfe eines Systems von Kameras und Spezialbrillen entsteht beim Betrachter das originalgetreue, dreidimensionale Abbild der Kabine. Alle generierten Daten werden im Format 1:1 abgebildet, und mit ein wenig Übung hat man tatsächlich den Eindruck, man könne sich in der künftigen Kabine frei bewegen.
In diesem 3-D-Modell kann man nun zum Beispiel herausfinden, ob etwa ein Schrank mit einem Türspant kollidiert, aber das klingt nicht gerade aufregend. „Ist es auch nicht,“ sagt Thomaschewski, „das ist Industriestandard. Viel spannender ist doch die Darstellung jener Installationen, die man später nicht sehen darf.“ So entwickelten die Teammitglieder mit Hilfe ihrer universitären Partner ein System, von dessen Funktionsfähigkeit sie überzeugt waren, aber nicht wussten, ob es auch tatsächlich funktioniert.
Erste Tests mit einzelnen Modulen am Kundenflugzeug
„Irgendwann mussten wir uns entschließen, mit der Arbeit anzufangen, und so begannen wir, an konkreten Flugzeugen einzelne Module auszuprobieren.“ Dabei war die Einbeziehung der Praktiker aus den Gewerken eine spannende Sache. Immerhin ist es für Ingenieure kein Problem, sich in einer dreidimensionalen Simulation zu bewegen, meint der Teamleiter, aber ein Tischler oder Klempner hat da schon eher Probleme. Dabei sind diese erfahrenen Kollegen jene, die oft schon beim ersten Blick auf eine Simulation eventuelle Fehler bemerken.
„Wir bekamen allerdings einfach nicht die erforderlichen Informationen“, erinnert sich Oliver Thomaschewski, weshalb sich das Team an das Institut für Betriebs- und Wirtschaftspädagogik der Uni Hamburg wandte. Die dortigen Spezialisten für Lernprozesse in Betrieben waren zuerst ganz schön überrascht, dass sie ausgerechnet aus der Luftfahrtindustrie um Hilfe gebeten wurden. Sie fanden aber die Probleme spannend und abwechslungsreich, und schließlich konnten die gewünschten Lösungen gefunden werden. „Mittlerweile kommen die Kollegen freiwillig vor dem Einbau und sehen sich eventuelle Problemfelder genau in der Simulation an. Diejenigen, die einst unsere größten Kritiker waren, sind jetzt unsere eifrigsten Befürworter.“
Flugzeuge sind lebendige Objekte
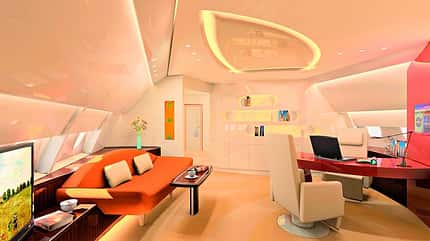
Welche Probleme sich bei der Erarbeitung der virtuellen Umwelt ergeben, sieht man zum Beispiel daran, dass ein Flugzeug sozusagen ein lebendiges Objekt ist. Da gibt es Durchbiegungen der Struktur in Abhängigkeit vom Beladungszustand, die Zelle bläht sich auf in Reiseflughöhe, im Sommer ist das Flugzeug plötzlich ein paar Millimeter länger usw.
Inzwischen hat das Team eine recht konkrete Vorstellung vom Endziel des Forschungsprojekts, aber noch ungefähr ein Jahr wird ins Land gehen, bevor die Kabine des ersten VIP-Flugzeugs komplett mit dem Virtual Fitcheck simuliert werden kann. Derzeit kann man jedes Standardrumpfflugzeug in der CAVE auf die Glaswände projizieren, und auch bei Großraumflugzeugen ist das kein Problem, nur dass man hier das virtuelle Modell nicht von Wand zu Wand begehen kann. Wer aber erst einmal den Umgang mit der Spezialbrille und der pistolenförmigen „Maus“ gelernt hat, bewegt sich sicher in dem dreidimensionalen Raum.
Der Nutzen des „Virtual Fitcheck“
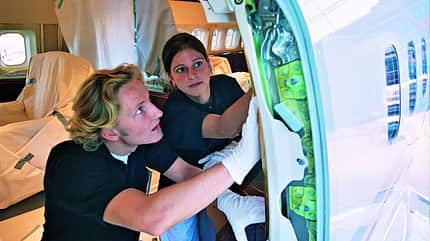
Welcher Nutzen ergibt sich nun aus der ganzen Forschungsarbeit? „In Geld kann man das kaum ausdrücken“, sagt Thomaschewski. Bestimmte Sachen lassen sich einfach nicht darauf reduzieren. „Viel wichtiger ist für uns, dass wir mit dem neuen System ein hohe Prozessstabilität erzielen.“
Welches Potenzial noch darin steckt, lässt sich zurzeit nur ansatzweise erkennen. Wenn jedoch zu guter Letzt ein Kunde sein Flugzeug in bester Qualität auch noch einige Wochen früher in Empfang nehmen kann, dann wird das wohl einen konkreten Nutzen ergeben.
FLUG REVUE Ausgabe 03/2012