Gehört hat jeder schon einmal vom 3D-Druck, manch einer hat schon ein gedrucktes Teil in der Hand gehabt, und einige wenige besitzen vielleicht sogar einen solchen Drucker, den sie vom heimischen PC aus ansteuern können. Man kann Spielzeug drucken, Schmuckstücke, bunte Kleinteile eben. Die Industrie aber denkt in anderen Dimensionen.
In der „Vor-Drucker-Zeit“ entwickelten Konstrukteure zahlreiche Bauteile, die wegen ihres komplizierten Aufbaus aus zahlreichen Einzelteilen bestehen und in aufwendiger Montage zusammengesetzt werden müssen. Teilweise ist das heute noch so, aber mehr und mehr gibt es Beispiele, wie man sich den Aufwand verringern, Zeit, Geld und vor allem Gewicht sparen kann. Experten sprechen vom „design for no assembly“, also dem Entwurf selbst komplexer Baugruppen, die in einem Arbeitsgang gedruckt werden können und keine Montageschritte mehr benötigen.
Bislang werden die gewünschten Teile nach genauen Zeichnungen beziehungsweise Computeranweisungen gegossen, gestanzt oder geschmiedet und dann mit viel Abfall weiterverarbeitet. Drehen, Bohren und Fräsen sind die hauptsächlichen Arbeitsschritte im Metallbau, während Plastikteile in der Regel per Spritzguss entstehen und mindestens entgratet werden müssen.
Präzisionsdruck aus Thermoplast oder Metall
Beim Drucken hingegen wird auf einer Grundplatte ein Teil Schicht für Schicht übereinander gedruckt, aus geschmolzenem Thermoplast, aber auch aus Metall. So entsteht praktisch kein Abfall, und die einzelnen Schichten werden mittlerweile derart präzise eine auf der anderen addiert (vom englischen Begriff „Additive Manufacturing“, AM), dass man sie selbst an glatten Flächen mit bloßem Auge nicht mehr erkennen kann.
Das Ganze klingt relativ einfach: Man fertigt Konstruktionszeichnungen an oder scannt eine Vorlage in Form eines bereits vorhandenen Teils. Zeichnungen oder Scans werden mit speziellen Computerprogrammen in Druckeranweisungen umgesetzt, in denen das gewünschte Teil in Abertausende dünne Schnitte zerlegt wird, welche jeweils einer Materialschicht entsprechen – und schon kann es losgehen.
Ganz so einfach ist das aber dann doch nicht, denn je nach Konfiguration des Endprodukts gibt es auch hier wieder unterschiedliche Verfahren. Man kann das Material zähflüssig aus Düsen pressen, wenn es um größere, kompakte Teile geht, oder dünnflüssig fein versprühen, ähnlich wie beim Nadeldrucker am PC. Das geht auch mit geschmolzenen Metallen, doch wird das eher selten genutzt. Metalldruck geschieht eher mittels des sogenannten Lasersinterns, indem per Laserstrahl feinstes Metallpulver genau dort geschmolzen wird, wo es benötigt wird, während alles Material ringsum unberührt bleibt. Zum Schluss kann man die Reste mit Druckluft einfach wegblasen und wiederverwenden – übrig bleibt ein hochkompliziertes Bauteil, das sogar Hohlräume einschließen kann.
Wenn also die Technologie in solch riesigen Schritten voranschreitet – werden wir dann tatsächlich bald in gedruckten Flugzeugen unterwegs sein? „Vielleicht“, sagt Nicole Clement, Marketingdirektorin bei Stratasys, einem der Pionierunternehmen des AM, „aber das wird wohl noch eine Weile dauern. Derzeit sind der Technik noch Grenzen gesetzt, in der Größe der Drucker und in der Dauer des Verfahrens.“ Üblicherweise kommt heute ein Kunde mit einer Zeichnung und will möglichst schnell ein Modell davon haben, um Form, Aussehen und Funktionalität überprüfen zu können. „Rapid Prototyping“ nennt man dieses Verfahren der schnellen Herstellung von Einzelteilen, aber schnell ist relativ. „Wenn alle Voraussetzungen stimmen, die Zeichnungen OK sind und wir freie Kapazität haben, dauert der Druck dennoch einen ganzen Tag, bei größeren und komplizierteren Teilen sogar noch etwas länger.“
Zurzeit geht es also vorrangig um Präsentationsteile, die nicht unbedingt langlebig sein müssen. Ist der Kunde zufrieden und wünscht die Serienproduktion, beginnt die Beratung bis hin zur Realisierung. Nicht immer ist der Seriendruck auch sinnvoll, wenn wir uns als Beispiel nur die Armlehne eines Passagiersitzes vorstellen. Hier wird einmal ein Werkzeug hergestellt und dann das Teil in sehr hoher Stückzahl per Spritzguss produziert. Das ist schneller und billiger als der Druck.
Für die Herstellung von Präsentationsstücken, von komplizierten Teilen und kleineren Serien allerdings lohnt sich wieder der Druck, denn man braucht kein Werkzeug, das sehr teuer ist und dessen Herstellung ziemlich lange dauert. Der größte Drucker kann derzeit Teile von 0,8 x 1,0 x 1,0 Metern drucken, wobei größere Baugruppen mittels Stecken oder Kleben möglich sind. Die komplette Struktur eines Flugzeugrumpfes mit allen Spanten, Stringern und sonstigen Versteifungen wird da wohl noch etwas warten müssen.
Einschränkungen gibt es auch noch bei den Materialien. Für den Druck geeignete Thermoplaste gibt es nicht sehr viele, obwohl schon in kurz- und langlebige unterschieden wird. Nur die Auswahl an Farben und Kombinationen ist beinahe unendlich – und der Druck von mehrfarbigen Teilen kein Problem.
Beim Druck von Metallteilen sieht es allerdings ganz anders aus, und das ist auch der Bereich, auf den sich die Luftfahrtindustrie konzentriert. Für das Lasersintern bieten spezialisierte Unternehmen Metallpulver in beinahe allen Zusammensetzungen an, von hochrein bis zur vom Kunden gewünschten Legierung, Ob Aluminium, Magnesium oder Titan, es gibt kaum ein Metall, das in irgendeiner Zusammensetzung nicht verwendet werden könnte. Ein Vorteil ist auch, dass man keine Ersatzteile auf Vorrat produzieren muss, denn bei Bedarf kann jederzeit nachgedruckt werden.
Wenn dabei von feinstem Pulver die Rede ist, so ist Mehl im Vergleich noch grobkörniger Kies. Taucht man eine Hand in solches Industriepulver, so fühlt es sich an wie eine Flüssigkeit (und später braucht man Tage, um das Zeug wieder aus allen Poren rauszukriegen). Nur so ist es möglich, das Material möglichst schnell aufzuschmelzen und mit der darunterliegenden Schicht zu verbinden, ohne dass es breitläuft.
Interessant ist auch die Möglichkeit des Druckens von Kohlenstoff-Bauteilen, nur dass hier der reine Kohlenstoff nicht in Fasern gezogen, sondern geschmolzen und als feiner Nebel versprüht wird, sodass wieder Schicht für Schicht Bauteile entstehen. Praktische Erfahrungen gibt es schon in der Automobilindustrie und hier vor allem bei den Formel-1-Rennern, wo es auf geringstes Gewicht, nicht so sehr allerdings auf das Geld ankommt.
Solche „gläsernen Flugzeuge“ wie auf unserem Aufmacherbild kommen also unter Umständen schneller, als wir uns das jetzt noch vorstellen können. Viele Unternehmen haben die Zeichen der Zeit erkannt und investieren enorme Summen in Forschung und Entwicklung. Für die Weiterentwicklung der Druckertechnik, einschließlich von Multifunktionsgeräten für den Druck kombinierter Materialien, gibt es jedenfalls bereits ambitionierte, weit in die Zukunft reichende Pläne, und schneller als gedacht fliegen wir „wie gedruckt“.
Gedruckte Teile: leichter, fester und billiger
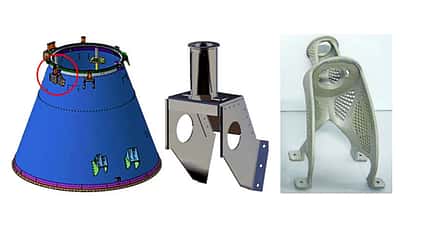
Das hier gezeigte Beispiel zeigt, wie gedruckte Teile bereits jetzt in der Praxis eingesetzt werden: Links sieht man die Baugruppe einer Raketenoberstufe, auf der die Nutzlast mittels spezieller Halterungen befestigt wird, von denen eine im roten Kreis markiert ist. In der Mitte ist solch ein Teil zu sehen, wie es bis jetzt in mehreren Arbeitsgängen gefertigt wurde. Es besteht aus vier Einzelteilen und wiegt 0,453 kg. Es wurde mehrfach optimiert, bis zum Schluss das rechts abgebildete Teil im sogenannten bionischen Design entstand, einteilig und nur noch 0,168 kg schwer. Die Bionik wiederum geht davon aus, dass es der Natur im Verlaufe der Evolution gelang, Prozesse und Strukturen an die Umgebung anzupassen und zu optimieren. Deshalb sieht das Endprodukt auch völlig anders aus als das Original, doch erfüllt es genau die gleiche Aufgabe. Weitere Optimierungen sind jetzt nur noch bei der Verwendung der Materialien möglich, die Form indessen bleibt.
FLUG REVUE Ausgabe 08/2015