Flugzeugbau - Kunststoff oder Metall?
Die Verwendung der verschiedensten Kunststoffe ist schon lange gängige Praxis im Flugzeugbau, doch hatte es sich dabei stets um Bauteile gehandelt, die keinen größeren Lasten während Start, Landung oder Reiseflug ausgesetzt waren. Nehmen wir das Beispiel Airbus: Beginnend bei der A300 bis zum heutigen Megaliner A380 wird die Seitenflosse aus einer Kunststoffstruktur gefertigt, die Halterungen jedoch, mit denen das Ruder angeschlagen wird, bestehen aus Titan. Boeing hatte nun mit der Ankündigung, in Gestalt des Dreamliners ein „Kunststoffflugzeug“ bauen zu wollen, scheinbar eine Grenze überschritten, die bis dahin von den Konstrukteuren nicht zu überwinden war.
Die Betonung beim vorhergehenden Satz liegt aber auf „scheinbar“, denn während der gesamten Entwicklungsphase und des Baus der ersten Exemplare zeigte sich, dass noch mehr als die Hälfte aller Baugruppen des neuen Musters aus Metallen besteht, und an diesem Anteil wird sich wohl auch bei den Modellen der nächsten Generation nicht viel ändern. Doch woran liegt es, dass auch auf absehbare Zeit noch Metalle benötigt werden, wo doch die Vorteile der Kunststoffe auf der Hand liegen – Leichtigkeit, Festigkeit und geringe Korrosionsanfälligkeit – um nur einige zu nennen?
Unglücklicherweise gibt es – noch – keinen Kunststoff, der beispielsweise Aluminium im Flugzeugbau vollständig ablösen könnte, denn die heutigen Kunststoffe sind einfach noch nicht fest und steif genug, auch wenn man während der Herstellung die Eigenschaften sehr weit variieren kann. Andererseits kann man die Steifigkeit mit faserverstärkten Kunststoffen so weit erhöhen, dass eine Ablösung von Metallen in einem gewissen Rahmen möglich ist.
Betrachtet man indessen die Technologie der Herstellung von Rumpfsektionen für die Boeing 787, dann zeigt sich, dass man hier noch lange nicht ohne Metall auskommt. Immerhin ist die CFK-Hülle im Durchschnitt nur sechs Millimeter dick und daher nicht selbsttragend.
Einbauten aus Metall vermindern die Gewichtseinsparung
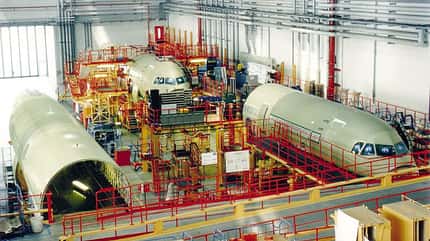
Erst die Installation zahlreicher Teile aus Metall sorgt für die notwendige Festigkeit und Stabilität. Hinzu kommt, dass man für das Zusammenfügen der Rumpfsektionen mehr Nieten benötigt, als das bei einem Metallrumpf der Fall ist, und während diese hier in der Regel aus Aluminium bestehen, müssen sie bei der 787 aus Titan sein. Kurz gesagt: Die Gewichtsvorteil bei diesem Flugzeug ist gar nicht mehr so groß, wie man anfangs angenommen hatte. Andererseits ist die Korrosionsfestigkeit viel höher und wiegt andere Nachteile wieder auf.
Einer dieser Nachteile ist, dass auch die Karbonfasern letztendlich auf Erdöl basieren. Die Wunderfasern, die achtmal so dünn wie ein menschliches Haar sind, benötigen im Herstellungsprozess Temperaturen von bis zu 2500 Grad Celsius, und der technologische Aufwand im Verbund mit dem Energieverbrauch macht den Werkstoff sehr teuer.
Noch viele weitere Kunststoffe werden, entsprechend ihrer bevorzugten Eigenschaften, an und in Flugzeugen verbaut. Hier seien stellvertretend nur Airbus-Flügelnasen von Ticona erwähnt, Flugzeugfenster aus Acryl, Decken- und Wandverkleidungen, Cockpittüren aus Kevlar und schließlich Fußbodenplatten oder Gepäckfächer aus Wabenmaterial.
Neue Legierungen mit Lithium, Kupfer und Silber
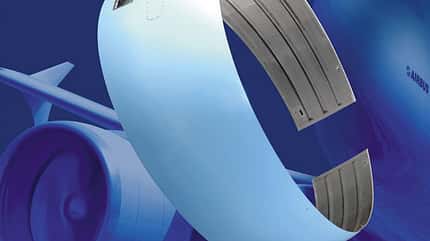
Ist also das Ende der Metalle im Flugzeugbau schon in Sicht? Noch lange nicht, sagen die Experten und verweisen auch hier auf neue Ergebnisse aus Forschung und Entwicklung. So werden seit einiger Zeit erfolgreich neue Legierungen aus Aluminium und Lithium eingesetzt, die viel leichter sind als frühere Verbindungen und damit erfolgreich einen Marktvorteil der Kunststoffe angreifen.
Constellium beispielsweise, früher als Alcan bekannt, entwickelte eine Legierung unter der Bezeichnung Airware, die etwas verwirrend nicht als Material, sondern als Technologie bezeichnet wird. Daraus gefertigte Bauteile haben einen höheren Anteil von Lithium, Kupfer und Silber (über die genaue Zusammensetzung schweigt man sich wegen der Konkurrenz aus), doch sollen sie bis zu 25 Prozent leichter als vergleichbare Teile aus konventionellen Legierungen sein.
Einfache Reparatur
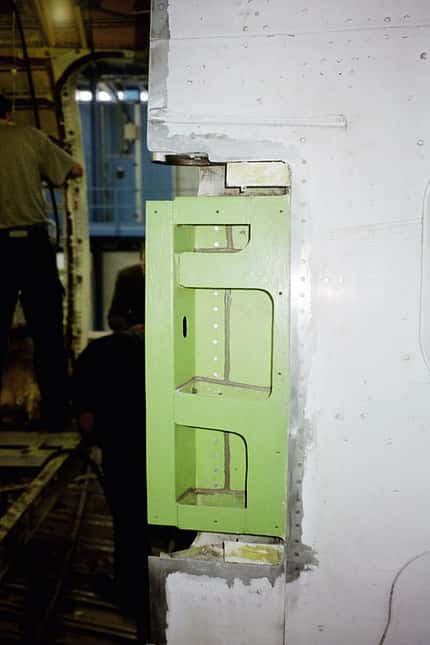
Unschlagbar ist schließlich derzeit noch das Verhalten von Metallteilen im Falle mechanischer Beschädigungen. Airlines und Wartungsbetriebe verweisen hier vor allem auf Schäden, die im Bodenbetrieb entstehen und oft genug in Folge des Zusammenpralls mit Servicefahrzeugen auftreten. Vor allem rings um Türen und Ladeluken entstehen so schnell Beulen oder gar Risse, die aber relativ leicht repariert werden können. Bei Kunststoffen ist das heute noch anders. Sie federn zwar heftige Stöße besser ab als Metalle, aber ab einer gewissen Grenze kommt es auch hier zum Bruch. Der jedoch ist nicht so leicht zu reparieren, und deswegen bevorzugen die Betreiber vor allem für Flugzeuge im Kurz- und Mittelstreckenverkehr die Metallbauweise.
Unterstützung dabei finden sie bei Marktprognosen von Alcoa, einem der größten Aluminiumproduzenten der Welt. Die nächste Generation von Schmalrumpfflugzeugen werde eine um rund 27 Prozent höhere Kraftstoffeffizienz aufweisen, wobei zwölf Prozent auf neue Legierungen und 15 Prozent auf verbesserte Triebwerke entfielen. Wenn also die Forschung nicht Kunststoffe mit völlig neuen Eigenschaften hervorbringt, werden die Metalle noch auf lange Zeit ihren Platz im Flugzeugbau behaupten.
FLUG REVUE Ausgabe 09/2011