Das Flugzeug mit dem höchsten Anteil an kohlefaserverstärktem Kunststoff (CFK) ist der Airbus A350 XWB. Flügel, Leitwerk und ein Großteil des Rumpfs: 53 Prozent des Zweistrahlers bestehen aus dem leichten und dennoch festen Werkstoff. Doch nach wie vor ist die industrielle Fertigung großer CFK-Bauteile zeitintensiv und teuer.
Forschungseinrichtungen wie das Fraunhofer IFAM in Bremen und Stade arbeiten deshalb mit Industriepartnern an Lösungen für eine effizientere Herstellung und Verarbeitung. Dazu gehören beispielsweise parallel arbeitende Montageroboter, mobile Roboter zum Umrissfräsen, aber auch plasmabeschichtete Trennfolien, um Großstrukturen aus Faserverbundwerkstoffen trennmittelfrei fertigen zu können.
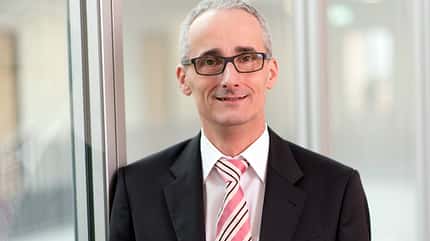
Ganze Flugzeuge aus CFK wird es nach Einschätzung von Prof. Dr. Bernd Mayer, Leiter des Fraunhofer IFAM, dennoch in Zukunft nicht geben: „Im Flugzeugbau geschieht nun das, was in der Automobilbranche seit Jahren praktiziert wird: Man konzentriert sich auf Materialkombinationen.“ Flugzeughersteller werden sich nun eher anschauen, an welchen Stellen welche Anforderungen gelten und entsprechend das optimale Material suchen, ob Metall oder Verbundwerkstoff.
Neue Verbundwerkstoffe in der Entwicklung
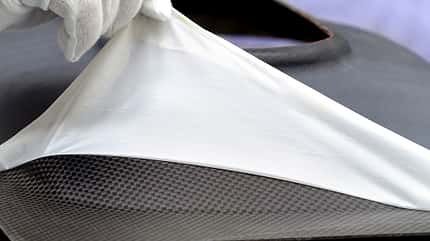
Fortschritte gab es in den vergangenen Jahren auch bei der Erkennung von Schäden an Verbundwerkstoffen. „An den Material-Schnittstellen ist das Risiko höher, dass Defekte auftreten“, so Prof. Mayer. Doch mit Ultraschall und Thermografie könnten Schäden effizient und schnell gefunden werden. „Auf wissenschaftlicher Basis weiterentwickelt wurde auch die Röntgentomografie“, sagt Prof. Mayer. Die Methode sei zwar bisher zeitaufwendig und daher nur schwer in den Fertigungsprozess integrierbar, liefere aber sehr präzise Informationen.
Und auch an neuen Composite-Materialien wird geforscht. Interessant sind vor allem thermoplastische Verbundwerkstoffe. Hierbei werden Fasern, beispielsweise aus Glas oder Carbon, in eine Matrix aus thermoplastischen, das heißt in einem spezifischen Temperaturbereich verformbaren, Kunststoffen eingebettet. „Thermoplastische Verbundwerkstoffe sind einfacher in der Verarbeitung als die bisherigen Verbundwerkstoffe“, sagt Prof. Mayer. Es sei keine aufwendige und teure Anlagentechnik wie ein Autoklav nötig. Glasfaserverstärktes Polyamid beispielsweise wird bereits heute für Verstärkungselemente in der Automobilbranche eingesetzt. „Die Entwicklung bei Verbundwerkstoffen hört nicht auf“, sagt Prof. Mayer.