Vor allem an einem der „Arbeitspferde“ des Kurz- und Mittelstreckenverkehrs, der Boeing 737NG, kann man die auffällig nach oben verlängerten Flügelspitzen immer häufiger sehen. Aber auch an den Tragflächenenden anderer Flugzeugtypen sind sie in den unterschiedlichsten Formen und Größen angebracht. Dabei waren die „langen Ohren“ bei der 737 ursprünglich gar nicht als aerodynamische Hilfsmittel gedacht, sondern entstanden in Folge von Wünschen gut betuchter Privatkunden, die für ihre Jets auffällige Unterscheidungsmerkmale gegenüber „normalen“ Flugzeugen suchten.
Als dann 1991 die ersten Business Jets des Typs Gulfstream II mit Blended Winglets von Aviation Partners ausgestattet wurden, sollten sie einfach nur eleganter aussehen, doch stellte sich zur Überraschung der Konstrukteure heraus, dass die nach oben verlängerten Flügel nicht nur Sprit einsparten, sondern durch eine bessere Steigrate auch den Fluglärm verringerten. Dabei muss man die Konstrukteure wohl in zwei Gruppen unterteilen, in jene von Aviation Partners unter Dr. Bernie Gratzer, welche die Winglets entwickelt hatten und aufgrund der Versuche im Windkanal von deren Vorteilen überzeugt waren, und die Ingenieure, welche die Tragflächen der Luftfahrzeuge konstruiert hatten. Diese vertraten anfangs die Meinung, den optimalen Flügel geschaffen zu haben, und sahen in den Winglets nur unnützen Ballast, einen Spleen der Eigentümer sozusagen.
Enorme Einsparungen gegenüber dem Standard
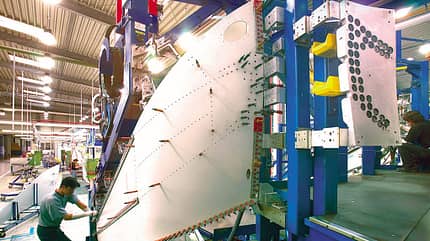
Da der Kunde aber König ist, wurden immer mehr Maschinen mit Winglets ausgerüstet, immer noch eher des eleganten Aussehens wegen denn der Sparpotenziale – die standen bei den privaten Betreibern ohnehin im Hintergrund. Als dann erstmals die überraschenden Spar-Zahlen bekannt wurden, wollte sie zuerst keiner der Fachleute glauben: Zwischen 360.000 und 490.000 Liter Kraftstoff pro Jahr, je nach geflogenen Strecken, kann eine mit Winglets ausgerüstete Boeing 737NG gegenüber einem Standardmodell einsparen, gab Joe Clark, der Chef der Aviation Partners, bekannt. Doch die Zahlen ließen sich belegen.
Nun begann ein Ansturm von Fluggesellschaften die von den Einsparungen profitieren wollen. Hapag-Lloyd und airberlin waren die ersten. „Rund 800 Einheiten liefern wir jährlich aus, und inzwischen gibt es mit dem Kunden auch Gespräche über eine mögliche Fertigung von Winglets für die 737 Classic,“ berichtet stolz Robert Machtlinger, Vice President Structures bei der Fischer Advanced Composite Components AG (FACC) im oberösterreichischen Ried. Hier ist Southwest Airlines mit einer der weltweit größten 737-Flotten der Launch Customer, und die Fertigungsrate liegt bei rund 200 Einheiten im Jahr.
Weniger Luftwirbel – weniger Fluglärm
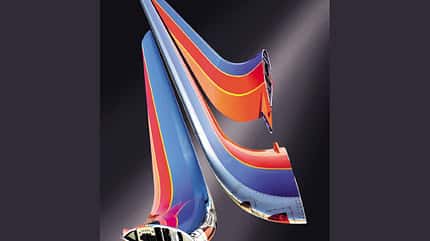
Dabei ist die Wirkungsweise von Winglets schon lange bekannt, versucht man doch damit die Luftströmung an den Flügelspitzen zu beeinflussen. Deren Eigenart besteht nämlich darin, dass die den Flügel an der Oberseite umströmende, schnellere Luft zu den Flügelspitzen hin abfließt, während der Vektor der langsam strömenden Luft an der Flügelunterseite nach innen gerichtet ist. An den Flügelspitzen selbst bilden sich spiralförmige Wirbel durch die Vermischung langsamer und schneller strömender Luft, und ein aerodynamisch sauberes Winglet kann diese Verwirbelungen auffangen, indem es das Abfließen der Luft nach außen verhindert und die Luftströmung in einen nach hinten gerichteten Fluss zwingt. Die Resultierende daraus ermöglicht einen höheren Auftrieb und damit die enorme Kraftstoffeinsparung, und weniger Luftwirbel verursachen zudem weniger Fluglärm. Grund genug für die Airlines, ihre Maschinen mit den „Hilfsflügeln“ nachzurüsten, und die Boeing-Manager waren Geschäftsleute genug, dass sie sich nun mit den Aerodynamikern von Aviation Partners zusammentaten.
Eine 757 spart fast eine Million Liter Kraftstoff pro Jahr!
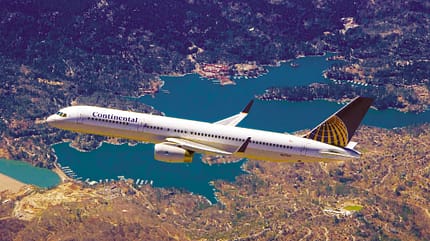
Inzwischen vermarktet Aviation Partners Boeing (APB) die Technologie gemeinsam, und viele Airlines lassen sich ihre neuen 737NGs bereits mit Blended Winglets ausliefern. Selbst neue Marktsegmente hat man dabei schon angepeilt, wie zum Beispiel die Boeing 757. Obwohl deren Produktion nach 1050 Exemplaren inzwischen eingestellt worden ist, werden solche Maschinen noch lange fliegen und sollen künftig ebenfalls sparsamer eingesetzt werden.
Etwa 540 Flugzeuge kommen dafür in Frage. Der erste Auftrag dazu kam von Continental, die 20 Shipsets fest bestellte und auf weitere 20 Optionen hält. Aviation Partners und FACC haben zwischen Juni und Dezember 2004 die Entwicklung der Winglets für die 757 abgeschlossen, an der sich FACC mit einer Investition in Höhe von 7,5 Millionen Dollar beteiligt hat. Auch an den Tests und der nachfolgenden Qualifizierung hat sich FACC finanziell beteiligt. Das Unternehmen muss nunmehr anbauen, um alle Aufträge termingerecht abzuarbeiten, und Mitarbeiter kommen selbst über 50 Kilometer Entfernung aus Bayern. „Mittlerweile macht die Produktion der Winglets rund ein Viertel unseres Geschäfts aus“, berichtet Robert Machtlinger.
CFK-Bauteile entstehen in Handarbeit
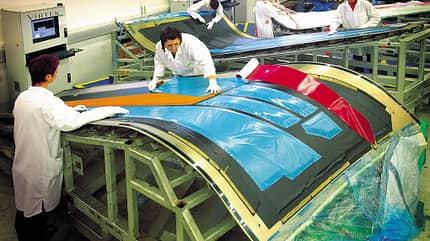
Ein Blick in die Fertigungsstätte offenbart dann auch geschäftiges Treiben. Zuerst tragen im Reinraum eingespielte Teams die vorgefertigten, mit Harz imprägnierten Lagen aus Kohlefasermaterial auf, drücken sie Schicht für Schicht unter heißer Luft in die Form, umhüllen sie anschließend mit Folie, damit eventuelle Lufteinschlüsse abgesaugt werden können. Eine mühselige, anstrengende Handarbeit, denn es gibt noch keine Maschinen für diese Tätigkeit. „Weltweit ist der Bedarf an CFK-Matten stark angestiegen, so dass die Preise in den letzten Jahren regelrecht explodiert sind“, gibt Machtlinger Auskunft. „Wir haben zudem Fixpreise mit Boeing vereinbart, konnten aber die Preissteigerungen beim Rohmaterial bisher durch Rationalisierungen auffangen.“
Derzeit durchlaufen täglich drei Shipsets die Taktlinie, und auch deshalb ist höchste Qualität angesagt. Das Material wie auch das Zubehör werden pünktlich angeliefert, und die Auslieferung erfolgt ebenso streng nach Plan. Eine Zwischenlagerung wäre teuer und ist deshalb gar nicht erst geplant. Fehlerhafte Arbeit würde daher den ganzen Betriebsablauf empfindlich stören, weshalb nach jedem Arbeitsschritt gründliche Kontrollen angesagt sind, die in umfangreichen Begleitdokumenten für jedes Teil nachgewiesen werden.
Nach dem rund achtstündigen Backen der Halbschalen im Autoklaven gelangen die Teile zur Taktstraße. Hier werden Rippen zur Stabilisierung eingezogen, die Anschlussflansche für den Flügel montiert und Positions- sowie Blinklichter samt der dazugehörigen Verkabelung installiert. Zwischendurch immer wieder Kontrollen, so in einer speziellen Anlage, die per Laserstrahl mögliche Verspannungen registriert. Schließlich erfolgten das Zusammenfügen der Schalen und das Anbringen der polierten Metallschienen an den Stoßkanten der nun etwa 65 Kilogramm wiegenden Winglets. 600 unterschiedliche Schrauben und Bolzen halten das Ganze zusammen. Vier Tage dauert die Herstellung der Einzelkomponenten, fünf Tage die Endmontage. Alle fünf Stunden wird ein komplettes Shipset, also ein Paar Winglets, fertig gestellt.
Die Umrüstung dauert nur 72 Stunden
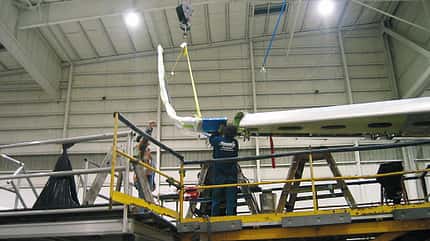
Den Abschluss bildet die Lackierung in den Kundenfarben, und ausgeliefert wird per Luftfracht an Boeing, aber nur für jene Neubauten, die bereits mit Winglets an die Kunden gehen. Nachrüstungen hingegen werden in Werften in aller Welt durchgeführt, so dass auch hier nach einem genau ausgeklügelten Zeitplan geliefert werden muss. Immerhin sollen die Bauteile genau dann zur Umrüstung bereitstehen, wenn das dafür vorgesehene Flugzeug in die Halle rollt. Jetzt werden die originalen Flügelspitzen entfernt, die Flügelstrukturen verstärkt, die Bordelektrik nachgerüstet und die Winglets montiert. 72 Stunden später kann die Maschine abheben, mit rund 200 Kilometern größerer Reichweite und um 6,5 Prozent verringerten Start- und Landegeräuschen gegenüber vorher. Da sind sogar Flüge möglich, wenn andere Flugzeuge wegen der Nachtflugbeschränkungen oder geringerer Steigraten am Boden bleiben müssen.
Bei all dem Aufwand und der ausgeklügelten Technologie gibt es inzwischen in Ried sogar noch Kapazitäten für Reparaturen, denn es kann passieren, dass Winglets im Betrieb am Boden mechanische Beschädigungen erleiden. Und die Zukunft? Für die 767 kann man sich ebenso Blended Winglets vorstellen, vielleicht sogar für Airbusse. Doch das müssen die Hersteller entscheiden und die Kunden wollen.
FLUG REVUE Ausgabe 11/2006