Halle 9 auf dem Airbus-Werksgelände in Finkenwerder ist so etwas wie ein Kreißsaal für A320. Auf der Endmontage-Linie 2, einer von vier in Hamburg, werden die Airbus-Bestseller geboren. Bis ein neuer Narrowbody flügge ist, dauert es rund acht bis zehn Wochen. Dann ist nicht nur Mutter Airbus stolz, auch die vielen anderen Elternteile sind es. Denn rund 60 Prozent eines A320 stammt von Zulieferern.
Second Source Supplier
Airbus arbeitet mit mehr als 12 000 Lieferanten weltweit zusammen. Viele davon sind in Deutschland und Österreich beheimatet (eine Auswahl stellen wir auf der folgenden Doppelseite vor). Manche sind alleinige Zulieferer eines bestimmten Bauteils, andere sogenannte Second Source Supplier.
"Zulieferer sind für uns sehr, sehr wichtig", sagt Gerd Weber, Leiter der A320-Endmontage. "Viele Teile können wir als Flugzeughersteller gar nicht selbst bauen, beispielsweise die Triebwerke." Für die A320neo liefern das Leap-1A von CFM International und das PW1100G-JM von Pratt & Whitney den Schub. An Letzterem hält der deutsche Hersteller MTU Aero Engines 18 Prozent Programmanteil. In der bayerischen Landeshauptstadt ist zudem eine von weltweit drei Endmontagelinien für den A320neo-Getriebefan beheimatet. In ihren Aufbau hat die MTU rund 25 Millionen Euro investiert. Die Triebwerke werden aber so spät wie möglich am Flugzeug installiert, bevor es lackiert wird. Im Anschluss geht es zur Flightline, das heißt, es hebt zum ersten Testflug ab.
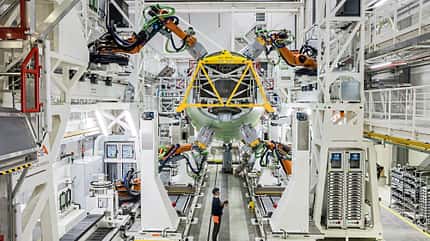
Endmontage im Takt
Doch zurück zum Anfang. Linie 2 beginnt mit Station 41. Hier kommen Rumpfvorder- und Hinterteil getrennt an und verlassen den Bauplatz als Einheit. Das Vorderteil kommt aus Saint-Nazaire und besteht aus Schalen der französischen Airbus-Tochter Stelia Aerospace, das Hinterteil entsteht in Hamburg in der Strukturmontage aus Zuliefererteilen von RUAG Aerostructures und Premium Aerotec. Airbus will die Flugzeugstruktur-Montage aber neu aufstellen, wie der Konzern im April mitteilte. In Deutschland sollen die Aktivitäten von Airbus in Stade sowie die Strukturmontage in Hamburg mit denen der Airbus-Tochter Premium Aerotec in Nordenham, Bremen und teilweise in Augsburg zusammengeführt werden.
Vom Data Management Computer bis zur Kabinenbeleuchtung
Bevor Airbus-Mitarbeiter die beiden großen Rumpfteile in der Station 41 verbinden, werden die großen Monumente – Bordküchen und Toiletten – in das offene Rumpfhinterteil gestellt. Ein wichtiger deutscher Zulieferer von Galleys und Lavatories ist Diehl Aviation. Diehl steuert aber viele weitere Elemente zur A320-Familie zu: vom Data Management Computer bis zur Kabinenbeleuchtung. "Unsere Standorte haben die A320-Familie ihr ganzes Programmleben lang unterstützt – und wir werden das auch in der Zukunft tun. Mit den steigenden Stückzahlen seit den 1980er Jahren nahm die Bedeutung der Baureihe auch für uns stetig zu", sagt Harald Mehring, Chief Customer Officer und Mitglied des Bereichsvorstands von Diehl Aviation. Man freue sich auf einen Wiederanstieg der Produktionsraten.
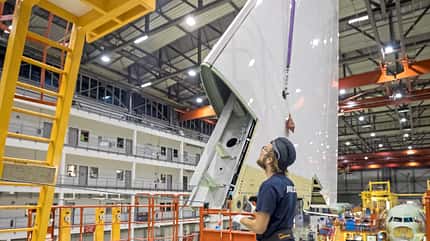
Qualifiziertes Personal
Pandemiebedingt hatte Airbus im April 2020 die Produktion auf den weltweit acht Endmontagelinien von 60 auf 40 Flugzeuge pro Monat heruntergefahren. Ein herber Schlag auch für die Zulieferer, die zuvor hart gearbeitet hatten, um die hohen Raten zu ermöglichen. Von Oktober an sollen wieder 45 Flugzeuge monatlich gebaut werden. Airbus forderte kürzlich die Zulieferer auf, bis zum zweiten Quartal 2023 eine feste Rate von 64 zu sichern. "Qualifiziertes Personal und entsprechendes Training spielen eine Schlüsselrolle. Das gilt für die gesamte Industrie, Airbus ebenso wie die Zulieferer", sagt Weber.
Teil für Teil entsteht ein Jet
Wenn die großen Rumpfteile auf Transportwagen in die Endmontage rollen, sind bereits viele Bauteile und Systeme (beispielsweise Kabel und Rohre) von Zulieferern integriert. Das geschieht in der Struktur- und Ausrüstungsmontage, die in anderen Hallen auf dem Airbus-Gelände untergebracht sind. Die Bodenpaneele für den Passagierraum sind zum Beispiel bereits größtenteils in den Sektionen verbaut. Zugeliefert werden die aus kohlefaserverstärkten Kunststoffen hergestellten Sandwichplatten seit 1995 von den Elbe Flugzeugwerken (EFW) aus Dresden.
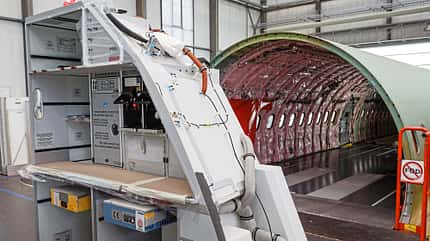
Klassisches Lieferantenverhältnis
An Station 41 ist auch schon das vordere Frachttor im Rumpfbug eingebaut. Rund 80 Prozent aller Tore und Türen an Airbus-Jets stammen von Airbus Helicopters aus Donauwörth. An der A320 ist das Schwesterunternehmen von Beginn an beteiligt. Die Zulieferer für die Tor-Hauptkomponenten und -Strukturen kommen aus Spanien, Südkorea, den Niederlanden und Österreich. In Donauwörth sind in der Produktion der Frachttore für die A320-Familie 45 Mitarbeiter beschäftigt, weitere 35 in Mexiko. Vorteile aus der gemeinsamen Konzernzugehörigkeit gebe es nicht. "Airbus Helicopters steht in klassischem Lieferantenverhältnis mit Airbus und stellt sich damit ständig einem interna-tionalen Wettbewerb", sagt der Pressesprecher Gregor von Kursell.
Performance des Flugzeugs
Die Rumpfröhre wandert nach vier Tagen weiter zur Station 40. Hier findet die "Hochzeit" statt: Die Flügel werden montiert. "Das ist der schwierigste Arbeitsplatz, teilweise geht es sehr eng zu. Und wir bestimmen hier letztlich die Performance des Flugzeugs. Wenn die Tragflächen nicht einwandfrei montiert sind, kostet das im Betrieb viel Treibstoff. Nur die erfahrensten Mitarbeiter kommen hier zum Einsatz", sagt Weber. Die Flügel werden von Airbus aus Broughton geliefert. Viele Komponenten von Zulieferern sind schon verbaut, beispielsweise Aktuatoren für die Flugsteuerung von Liebherr-Aerospace aus Lindenberg. Montiert werden dann auch die Sharklets, sie kommen unter anderem vom österreichischen Luftfahrtzulieferer FACC. In der Station 40 werden zudem Bug- und Hauptfahrwerk installiert.
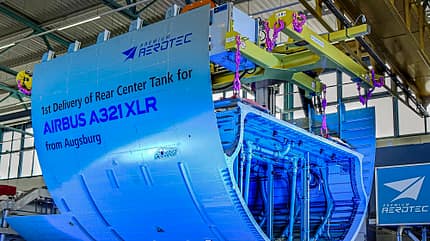
"Power-on"
Wieder vier Tage später rollt das Flugzeug nun "auf eigenen Beinen", wie Weber sagt, zur Station 35. Hier werden unter anderem das Höhen- und Seitenleitwerk integriert, die Heckspitze inklusive der APU angebracht und die inneren Landeklappen montiert. Airbus-Mitarbeiter stellen elektrische und hydraulische Systemverbindungen an der Trennstelle zwischen Flügel und Rumpf her. Auch das Klimapack von Liebherr-Aerospace aus Toulouse kommt hier in den Flugzeugbauch. Vorne an der Nase finden Radom und Wetterradar Platz. Auch die Arbeiten in der Kabine beginnen: Die Handgepäckfächer und Decken sowie Seitenverkleidungen werden montiert. Die in der ersten Station eingestellten Monumente werden nun verbaut. Mit dem "Power-on" beginnt in der Station 35 das elektrische und elektronische Herz der A320 zu schlagen.
Vier Tage später geht es zu Station 25. Hier werden Verkleidungselemente, beispielsweise zwischen Flügel und Rumpf, und die inneren Vorflügel montiert, das Kraftstoffsystem wird installiert. In die Kabine halten Trennwände Einzug, Teppichböden werden verlegt, Fluchtbeleuchtung und Türverkleidungen angebracht.
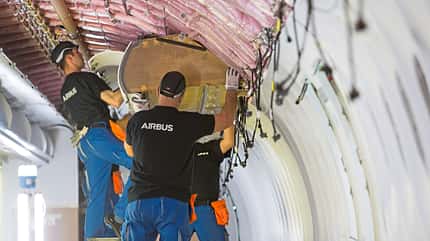
Feinschliff zum Schluss
In dieser vierten und letzten Station vor Verlassen der Halle 9 stehen auch zahlreiche System- und Funktionstests auf dem Plan: Elektrik, Hydraulik, Klimasystem und die mechanische Flugsteuerung werden geprüft, zudem findet der Kabinendrucktest statt.Ganz fertig ist das Flugzeug am Ende der Linie 2 noch nicht. Es fehlen, wie schon erwähnt, noch die Triebwerke. Und auch die Sitze und Sicherheitsgurte werden erst bei Station 23 in einer anderen Halle eingebaut. Manchmal kommt es auch vor, dass beispielsweise die Monumente aufgrund von Lieferverzögerungen nicht rechtzeitig ankommen. Dann müssen sie mühevoll zerlegt, in Einzelteilen durch die enge Kabinentür gebracht, auf- und eingebaut werden. Für solche Fälle gibt es einen Restarbeitsbauplatz. Aber wie es eben mit Babys so ist: So ganz fertig sind auch sie noch nicht, wenn sie zusammen mit ihren stolzen Eltern aus dem Kreißsaal kommen.
Arbeitsteilung
An der A320-Familie sind verschiedene Airbus-Standorte beteiligt. Eine Auswahl von Zuliefererbauteilen aus Deutschland und Österreich stellen wir mit Bild und Steckbrief vor.
Kabineninterieur, Avionik
- Diehl Aviation, u. a. Laupheim, Überlingen, Hamburg
- u. a. Rohre für Klimaanlage und Mischeinheit, Seitenwände, Data Management Computer, Kabinenbeleuchtung, Wassersystem, Rauch- und Feuermelder, Waschräume und Trennwände, Galleys (Retrofit)
- Diehl ist seit Beginn des A320-Programms Zulieferer
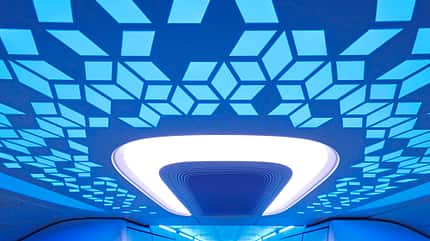
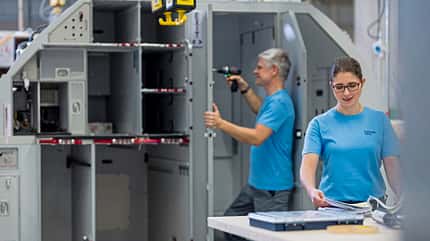
Rumpfsektionen
- RUAG Aerostructures, Oberpfaffenhofen, Emmen (CH) und Eger (HU)
- Integration Sektionen 18 und 19 (kommt teils von Turkish Aerospace), Fertigung Sektion 19.1, Fußboden, hinteres Druckschott und Seitenschalen der Rumpfmittelsektion
- RUAG hat nach eigenen Angaben bislang Rumpfsektionen für mehr als 9000 Flugzeuge der A320-Familie ausgeliefert
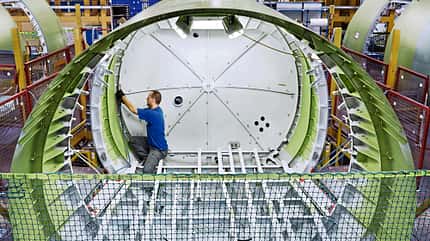
Vorderes Frachttor
- Airbus Helicopters, Donauwörth
- Das Airbus-Schwesterunternehmen produziert in Deutschland Türen und Tore für alle Airbus- Passagierflugzeuge (auf dem Foto A350), darunter das vordere Frachttor für die A320-Familie
- Der Standort Donauwörth ist seit Beginn des Single-Aisle-Programms als Lieferant beteiligt
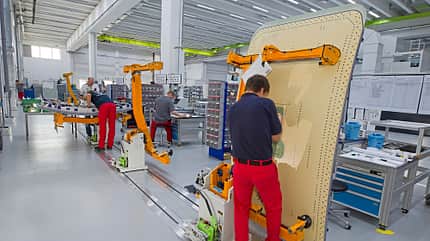
Rumpfschalen und -sektionen
- Premium Aerotec, Augsburg, Nordenham
- u. a. Fertigung Super- und Seitenschalen für Sektion 17 sowie weiterer großer Teile für Sektion 15 (Nordenham); Fertigung Rumpftank für A321XLR (Augsburg, Foto)
- Premium Aerotec ist eine 100-prozentige Airbus-Tochter
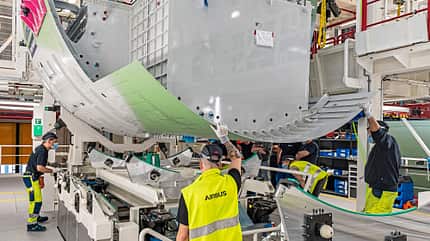
Triebwerk
- MTU Aero Engines, München
- erste vier Stufen des Hochdruckverdichters, schnelllaufende Niederdruckturbine, Bürstendichtungen für das PW1100G-JM, Endmontage eines Drittels der A320neo-Getriebefans in München
- MTU war schon ab den 1980ern mit dem IAE V2500 am A320-Programm beteiligt
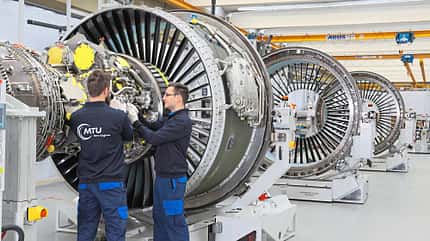
Luftmanagement, Flugsteuerung
- Liebherr-Aerospace, Lindenberg (Foto, vor Corona aufgenommen) und Toulouse (F)
- u. a. Hochauftriebssystem, Seitenruder-Servosteuerung, Klimatisierungssystem, Triebwerkabzapfluftsystem
- Erster Auftrag für das A320-Programm war 1984 über Entwicklung und Fertigung der Klimaanlage
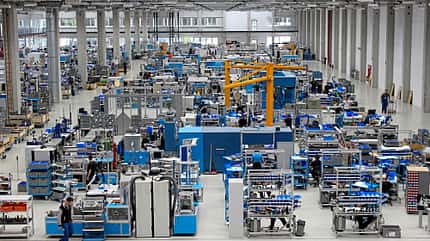
Fußboden, Kabineninterieur
- Elbe Flugzeugwerke (EFW), Dresden
- u. a. Floor Panels für den Passagierraum, Frachtraumverkleidungen, Trennwände mit integrierten Sitzen für Flugbegleiter (seit 2017) und beschusssichere Cockpittüren
- EFW ist seit 1995 Lieferant für die A320-Familie
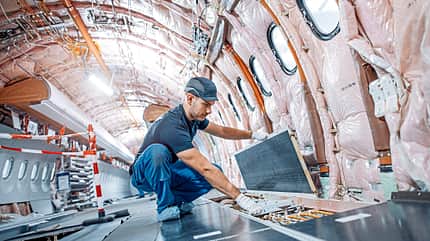
Passagiersitze
- Recaro Aircraft Seating, Schwäbisch Hall
- u. a. Economy-Class-Sitze BL3510, BL3530
- Erster Economy-Class-Kurzstrecken-Sitz 3410 ab Anfang der 1990-er Jahre für die A320-Familie
- Welcher Sitzhersteller zum Zug kommt, entscheidet die Airline
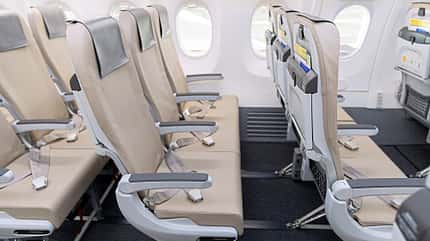
Strukturbauteile, Kabineninterieur
- FACC, Ried im Innkreis (AU)
- u. a. Winglets (werden auch von Korean Air hergestellt), Flügel-Rumpf-Verkleidungen, Staulufteinlässe, Landeklappen (nur A321), Gepäckablagefächer, Decken und Licht-Paneele
- 1989 erster Fertigungsauftrag für A320
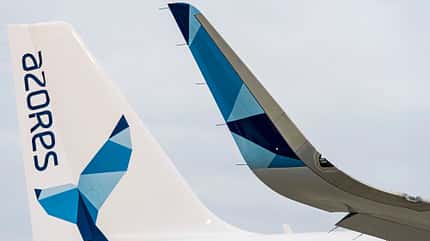
Sicherheitsgurte
- Schroth Safety Products, Arnsberg
- jährlich produziert Schroth rund 40000 Passagiergurte, Gurtsysteme für Flugbegleiter sowie VIP-Gurte (Airbus Corporate Jets) für Flugzeuge der A320-Familie
- Seit 1998 ist Schroth A320-Zulieferer
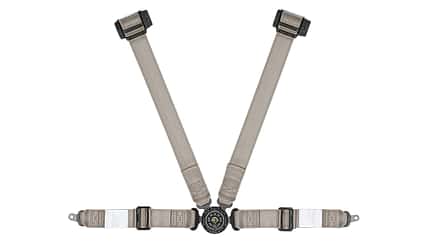
Herausforderung A321XLR
Airbus arbeitet derzeit an einer neue Top-Version der A320neo-Familie: der A321XLR, die mit 8700 Kilometern Reichweite ein veritables Langstreckenflugzeug werden soll. Dafür wird das Flugzeug mit einem fest installierten Tank im hinteren Rumpfteil, unterhalb des Fußbodens, ausgestattet. Dieser Rear Center Tank wird in die Sektionen 15 und 17 integriert. Gebaut wird er, ebenso wie die modifizierten Sektionen 15 und 17, von Premium Aerotec.
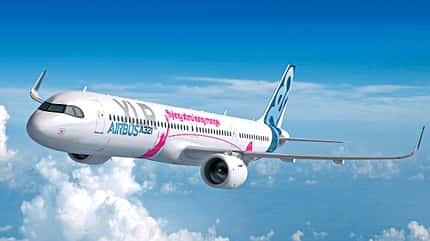
A321XLR-Pilotlinie
Zudem werden Struktur und Fahrwerk für das maximale Startgewicht von mehr als 100 Tonnen optimiert, das Flugzeug erhält stärkere Bremsen, neue, einteilige Landeklappen an den Innenseiten der Tragflächen und einen größeren Brauchwassertank. RUAG Aerostructures steuert die unteren Seitenschalen mit Fahrwerksschacht und Fußbodenstrukturen, die oberen Seitenschalen des Flugzeugrumpfes, die Druckkalotte und die Heckspitze bei, Diehl Aviation das Abwassersystem, FACC die überarbeitete Rumpfverkleidung. Um die reguläre A320-Strukturmontage nicht zu stören, hat Airbus in Hamburg in der früheren A380-Halle eine A321XLR-Pilotlinie aufgebaut, um die Fertigung der ersten Flugzeuge vorzubereiten.