Flugzeugsitze – leicht und sicher
Sitzentwicklung ist vor allem Komplexitätsmanagement“, beginnt Hartmut Schürg seine Erläuterungen. Er ist verantwortlich für die Produktentwicklung bei der RECARO Aircraft Seating GmbH in Schwäbisch Hall, einem der drei Großen des weltweiten Geschäfts mit den Flugzeugsitzen.
Mit der Ausstattung der Flugzeugkabinen von heute ist ein enormer Wettbewerb verbunden, weil sie den Passagieren – neben dem Service – als Einziges von ihrem Flug in Erinnerung bleibt. Jede Airline will, dass sich die Fluggäste mit dem Gefühl, angenehm geflogen und betreut worden zu sein, von Bord verabschieden und darum beim nächsten Flug auch wieder diese Fluggesellschaft wählen. Dabei spielt die Bequemlichkeit des Sitzes eine entscheidende Rolle.
„Vielleicht erinnern sich die Passagiere auch noch an Farbe und Qualität der Sitzbezüge“, sagt Schürg, „aber das ist dann auch schon alles. Für uns jedoch ist der Sitz ein spezielles Möbelstück, das innerhalb sehr enger technischer Grenzen realisiert werden muss, und das uns deshalb immer wieder vor sehr große Herausforderungen stellt.“ Eine eigene Abteilung mit Ergonomen ist daran beteiligt, Modellbauer erstellen per Rapid Prototyping die ersten Muster nach den Entwürfen der Designer, und schließlich kommt der Bereich Zulassung zum Zug, mit Gewichtsberechnungen, Stressanalysen und Tests, die denen der Automobilindustrie in nichts nachstehen.
Versionen
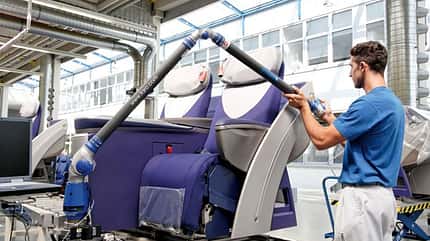
Sitze werden in Muster für Kurz- und Langstreckenflüge unterschieden, und dabei wieder in solche für Economy, Premium Line Economy, Business und First Class. Für die Kurzstrecke hat RECARO kundenunabhängig das Standardmodell Basic Line BL 3510 entwickelt, das es auch noch in einer Ausführung High Density gibt, für eine engere Bestuhlung. Dabei wurde die „Literaturtasche“ in das Kopfteil verlegt, damit sie nicht den Knien der Passagiere im Wege ist. Für die Langstrecke gibt es wieder ein Standardmodell, eine Premium Line und speziell für Britsh Airways Sitze der 4. Klasse, die optisch wie solche der Business Class aussehen, von der Struktur her aber denen der Economy Class entsprechen.
Die Kunden
Soweit zur Theorie. In der Praxis aber hat das Unternehmen rund 200 Airlines als Kunden, und die haben ganz eigene Vorstellungen und zahlreiche Wünsche, wie ihre Sitze aussehen sollen. „Hier toben sich dann die besten Designer der Welt aus“, sagt Hartmut Schürg voller Stolz, „wobei wir bestrebt sind, die Primärstrukturen zu erhalten.“ Also werden nur bestimmte Teile des Sitzes, wie beispielsweise die Armlehnen, für die individuelle Gestaltung freigegeben, während andere, für den Passagier meist nicht sichtbare, gleich bleiben. Das erleichtert in gewisser Weise die Durchführung der anspruchsvollen Zulassungsverfahren.
Inflight Entertainment
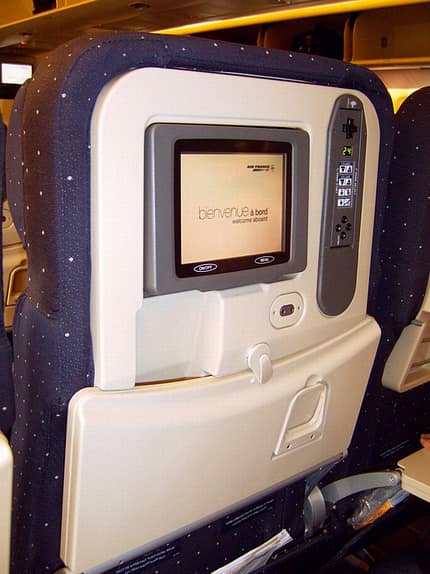
Ständige Treiber für die Entwicklung immer neuer Sitze sind die Elektronik, vor allem in Form des Inflight Entertainments, und die drängenden Forderungen der Kunden nach Gewichtseinsparungen. Je nachdem, für welchen Ausrüster sich die Airline bei der Bordunterhaltung entscheidet, müssen die Sitze entsprechend angepasst werden. Befindet sich zum Beispiel im Kopfteil des Vordersitzes ein Monitor, wollen manche Fluggesellschaften die dazugehörigen Fernbedienungen entweder gleich dort mit integriert haben oder aber auf beziehungsweise seitlich in der Armlehne, um nur ein Beispiel zu nennen.
Konzeption, Marktforschung und Entwicklung
Neue Konzepte gehen indessen nur in den Markt, wenn die Kosten und das Gewicht stimmen, eine Forderung, die für die RECARO-Entwickler nicht erst seit Einführung der A380 Grundlage aller Entwürfe ist. Dafür betreiben sie eine aufwändige Marktforschung und sind immer auf der Suche nach neuen Materialien, die die Abteilung Einkauf auch noch preisgünstig beschaffen soll. So gelang ihnen vor einiger Zeit die Entwicklung eines neuen Sitzes, der nur noch ein Tragrohr aus CFK anstelle der sonst verwendeten zwei aus Aluminium hat. Dadurch wurde Gewicht eingespart und zugleich dem Passagier mehr Beinfreiheit gewährt.
„Hervorragende Einzelwerkstoffe können aber in der Kombination plötzlich schlechtere Eigenschaften aufweisen“, sagt Hartmut Schürg, „doch auch die umgekehrte Wirkung tritt manchmal auf.“ Eine faszinierende Herausforderung an die Ingenieure, nach denen das Unternehmen dringend Ausschau hält. Hier bieten sich interessante Jobchancen für Luftfahrtingenieure oder Maschinenbauer. Alles in allem dauert die Entwicklung eines Standardsitzes, einschließlich der Zulassung, rund anderthalb Jahre, bei Kosten zwischen zwei und zehn Millionen Euro.
Zulassung
Beim Wort Zulassung kann Alfons Stachel, verantwortlicher Direktor dieses Bereiches, kaum noch an sich halten. Er bezeichnet sich selbst als „Überzeugungstäter“ mit langjähriger Erfahrung aus der Luftfahrtindustrie, von denen es bei RECARO viele gibt, und lässt die Begeisterung spüren, mit der er seine Arbeit macht.
Nach seinen Worten ist das Zuverlässigkeitsmanagement anspruchsvoller als das für die Flugzeugzelle, und dabei demonstriert er am Computer „nichtlineare Tools“ und neue numerische Crashsimulationen, deren Entwicklung kurz vor dem Abschluss steht. Sie sollen künftig die aufwändigen und teuren Crashtests ablösen.
„Für diese Tests verwenden wir die gleichen Dummys wie die Automobilindustrie“, sagt Stachel, „die mit einem Normgewicht von 77 Kilogramm etwa die Hälfte aller Passagiere repräsentieren.“ Der kleinere Rest ist leichter, die anderen sind schwerer, manche sogar viel schwerer. Da kann es schon einmal vorkommen, dass japanische Airlines anfragen, ob die Sitze für Sumoringer geeignet – und vor allem sicher - sind, die nicht nur eine komplette Dreierreihe und anstelle des Sicherheitsgurts einen Lastgurt in Anspruch nehmen, der wiederum an den äußeren Sitzenden befestigt wird. „Selbst für solche Extremfälle stellen wir spezielle Berechnungen an“, sagt Alfons Stachel, weil es dafür keine Dummys gibt, man aber andererseits solchen Menschen auch sicheres Fliegen bieten will.
Für alle aber gelten die gleichen Sicherheitsanforderungen, und bei den Tests müssen die Sitze Lasten von bis zu 16 g aushalten, ohne abzureißen, selbst dann, wenn das Flugzeug quer über die Bahn rutscht und dabei enorme Kräfte in der Querachse auftreten.
Sicherheit
Flugunfälle passieren überwiegend in der Start- oder Landephase eines Flugzeuges, und seit der Einführung der 16-g-Regel ist die Überlebensrate der Passagiere auf mehr als 90 Prozent gestiegen – vorausgesetzt, man hat den Sicherheitsgurt fest an-gezogen. Dafür werden die Sitze und ihre Einzelkomponenten unter statischen und dynamischen Gesichtspunkten getestet, nach der Sicherheit der installierten Elektronik und der Umweltverträglichkeit. „Es ist unglaublich, wie manche Passagiere ihre Sitze behandeln“, sagt Stachel kopfschüttelnd und verweist auf die extremen Anforderungen an den Leichtbau, ganz zu schweigen von Panikreaktionen im Evakuierungsfall. Da darf ein scheinbar graziler Klapptisch auch dann nicht brechen, wenn ein 90-Kilo-Passagier darüber klettert, und dass alle Materialien nicht entflammbar sein müssen, bedarf fast keiner speziellen Erwähnung mehr.
Besonders anspruchsvoll sind „Windmillingtests“, bei denen der Bruch einer Triebwerksschaufel simuliert wird. Das müssen zwar moderne Triebwerke aushalten können, aber sie laufen dann unrund und übertragen teilweise heftige Vibrationen auf die Zelle, die Kabine und damit auf die Passagiersitze. Da kann man schon einmal für längere Zeit unangenehm durchgerüttelt werden, doch die Sitze bleiben fest in ihren Verankerungen und sorgen dafür, dass die Fluggäste immer noch sicher bis zur Landung gebracht werden. Dass sie auch noch gut aussehen und zudem bequem sind, dafür geben rund 600 Mitarbeiter von RECARO die Garantie.
FLUG REVUE Ausgabe 03/2008