as Testprogramm hatte es in sich. 107 Stunden lang wurde der Getriebefan-Triebwerksdemonstrator auf dem Entwicklungsprüfstand von MTU in München auf Herz und Nieren untersucht und dabei auch bis aufs Äußerste strapaziert. Das Ziel: neue Technologien zu erproben, die den Antrieb noch effizienter machen. Denn der spezifische Treibstoffverbrauch soll noch einmal deutlich reduziert werden.
Dabei verbraucht das im Januar 2016 am Airbus A320neo (new engine option) eingeführte PW1100G-JM im Vergleich zum Referenz-Triebwerk IAE V2500 des A320ceo (current engine option) bereits 16 Prozent weniger Kerosin. „Wir streben an, bis 2030 minus 25 Prozent zu erreichen“, sagt Dr. Joachim Wulf, Chefingenieur Technologiedemonstratoren bei MTU. Kurzfristig soll der Kraftstoffverbrauch immerhin um zwei bis drei Prozent sinken.
Mit SAGE 4 (Sustainable and Green Engines, nachhaltige und grüne Triebwerke) verantwortet MTU einen von fünf Triebwerksdemonstratoren im europäischen Forschungsprogramm Clean Sky. Die Testläufe fanden von Oktober bis Dezember 2015 statt. Der US-Hersteller Pratt & Whitney stellte dafür ein PW1500G zur Verfügung, das normalerweise in der Bombardier C Series zum Einsatz kommt. Nach der detaillierten Datenauswertung, deren Ergebnisse kürzlich vorgestellt wurden, sind die MTU-Ingenieure zufrieden. „Wir haben zahlreiche neue Technologien getestet. Viele haben ihre Technologiereife unter Beweis gestellt. Einzelne Elemente sind bereits ready to fly“, sagt Dr. Jörg Henne, Leiter Entwicklung und Technologie bei MTU.
Der Fokus von SAGE 4 lag auf Neuerungen im Hochdruckverdichter und der schnelllaufenden Niederdruckturbine. Für beide Komponenten ist MTU bei der Getriebefan-Familie von Pratt & Whitney verantwortlich. Verbesserungspotenzial sehen die Ingenieure vor allem bei leichten und hitzebeständigen Materialien, neuen Herstellungsverfahren und Designanpassungen. „Wir wollten die Technologiereife neuer gewichtssparender Bauweisen und Materialien unter weiter gesteigerten mechanischen und thermischen Belastungen erbringen sowie den mechanischen Nachweis fortschrittlicher aerodynamischer Designs der Beschaufelung antreten“, so Wulf. Neue Simulationsmethoden und Messverfahren kamen ebenfalls zum Einsatz.
Entwickelt wurden die nun getesteten Innovationen seit 2008. „Damals haben wir erkannt, dass die Möglichkeiten des Getriebefans noch längst nicht ausgereizt sind“, sagt Technik-Vorstand Dr. Rainer Martens. MTU hat dabei mit mehr als 20 europäischen Partnern zusammengearbeitet, darunter kleine und mittlere Unternehmen wie die britische Firma Meggit Polymers and Composites, aber auch Hochschulen und Forschungseinrichtungen wie das iwb Anwenderzentrum Augsburg, der Technologietransferstelle des Instituts für Werkzeugmaschinen und Betriebswissenschaften (iwb) der TU München. „Wir gewinnen nicht nur neue Hardware, sondern auch neue Partner“, sagt Henne. In München wurde schließlich das sogenannte Supermodul montiert – bestehend aus der Niederdruckturbine von MTU, dem Turbinenaustrittsgehäuse des britisch-schwedischen Unternehmens GKN Aerospace sowie Welle und Lagerkammer von Pratt & Whitney – und in den P-1500G-Getriebefan integriert.
Neuartige Dichtungen im Hochdruckverdichter
Ein wesentlicher Beitrag zur Steigerung der Effizienz sind neue Dichtungstechnologien, die Strömungsverluste minimieren. Im Hochdruckverdichter von SAGE 4 wurden Dichtungsträger aus hochtemperaturfestem, kohlefaserverstärktem Kunststoff mit Teflonschaum erprobt. „Sie halten rund 100 Grad Celsius mehr aus als die bisher im Verdichterbereich eingesetzten Kunststoffe“, sagt Wulf. Gleichzeitig seien sie leichter und teilweise sogar günstiger in der Fertigung als Bauteile aus Metall. „Die Tests waren sehr erfolgreich. Wir haben die Dichtungsträger anschließend auf Risse und interne Beschädigungen geprüft und keine negativen Erkenntnisse gewonnen.“ Matthew Denmead, Entwicklungsingenieur bei Meggitt, ist überzeugt, dass sich das neue Material in Triebwerken durchsetzen wird: „Durch die deutliche Gewichtseinsparung haben Kohlefasern gerade in Hochtemperaturbereichen großes Potenzial.“
Zum Einsatz kamen im Hochdruckverdichter zudem additiv gefertigte Dichtungsträger aus einer Nickel-Basislegierung. Sie wurden bei Testläufen mit konventionellen Dichtungsträgern aus zusammengelöteten Blechen verglichen – ebenfalls mit positiven Ergebnissen. Solche gedruckten Dichtungsträger könnten schon bald per selektivem Laserschmelzverfahren in Serie gefertigt werden, so MTU.
Um den Wirkungsgrad des Hochdruckverdichters weiter zu verbessern, wurde auch der Strömungswiderstand verringert. Dafür wurden die Oberflächen von rotierenden und nicht-rotierenden Verdichterschaufeln poliert und mit einem Erosionsschutz versehen.
In der Niederdruckturbine wurde das Design der „Outer Cavities“ angepasst. Das sind die offenen Räume zwischen dem eigentlichen Gaskanal und den statischen Gehäusebauteilen, die üblicherweise mit Hilfe von Labyrinthdichtungen zwischen dem Gehäuse und dem äußeren Schaufeldeckband abgedichtet werden. „Dadurch können die Leckageströme besser kanalisiert und Strömungsverluste verringert werden“, sagt Wulf. Zudem wurde das Gehäuse überarbeitet und mit einer veränderten Kühlluftführung versehen. Die Ingenieure optimierten auch die Schaufeln aerodynamisch, was zu dünneren Kanten führt. Ebenfalls erprobt wurde ein neu entwickeltes Dämpfungssystem für die erste Laufschaufelstufe.
Nicht nur im Hochdruckverdichter, auch im Turbinenbereich wurden neue Dichtungstechnologien untersucht. „Erstmals haben wir in der schnelllaufenden Niederdruckturbine Bürstendichtungen eingesetzt“, erklärt Wulf. Bürstendichtungen bestehen aus tausenden Drähten, die mit einem Kerndraht in einem Klemmrohr fixiert werden. Die anströmenden Gase drücken diese Drähte gegen den Stützring und verdichten sie. Bisher wurden solche Dichtungen vor allem bei kleineren Durchmessern verwendet, wo die Relativgeschwindigkeit von bewegten zu statischen Teilen geringer ist.
Im Vergleich zu den üblicherweise verwendeten Labyrinthdichtungen hätten sie aber eine bessere Dichtwirkung, was den Gesamtwirkungsgrad des Triebwerks erhöhe. „Die Tests unter realen Triebwerksbedingungen mit maximaler Wärmeerzeugung im Dichtspalt waren erfolgreich“, sagt Wulf. Ebenfalls eine Premiere in der Niederdruckturbine hatten hitzeresistente, leichte keramische Faserverbundwerkstoffe. Bauteile aus CMC (Ceramic Matrix Composite) wurden bei SAGE 4 als Isoliersegmente im Triebwerksgehäuse verbaut.
Der Triebwerksdemonstrator durchlief auf dem größten Prüfstand bei MTU in München insgesamt 500 Zyklen, also jeweils Start, Hochfahren auf maximale Leistung sowie Landung beziehungsweise eine längere Leerlaufphase. „Jeder Zyklus schädigt die Bauteile. So bekommen wir einen Lebensdauernachweis“, erklärt Wulf. Bei den Testläufen wurde das Triebwerk mechanisch und thermisch auch jenseits der üblichen Limits von Serientriebwerken gefahren, um das Verhalten der neuen Technologien besser zu verstehen.
Einsatz in der nächsten Getriebefan-Generation
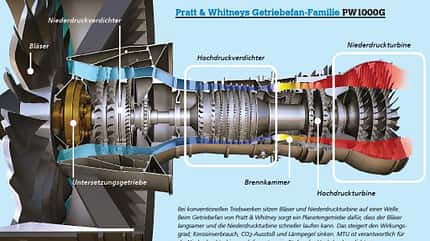
So wurde die Niederdruckturbine beispielsweise bei einem Stresstest auf 105 Prozent der zulässigen Drehzahl gebracht. „Das ist sehr spannend, weil wir Aufschluss über das Vibrationsverhalten bekommen“, sagt Wulf. Bei einem sogenannten Thermal Survey wurden die Bauteile bei Temperaturen oberhalb des regulären Betriebsbereichs bis zu sechs Stunden lang geprüft. Und bei einem „Rub-in Test“ legten es die MTU-Ingenieure auf einen besonders tiefen Einrieb zwischen Rotor und Gehäuse an. „Dadurch gewinnen wir Erfahrungen, ob die neuen Dichtungstechnologien das geforderte stabile Anstreifverhalten zeigen“, erklärt Wulf.
Insgesamt 600 Messstellen lieferten während der Erprobung Daten. Zwischen den Testläufen wurde das Triebwerk regelmäßig von außen und – mit Hilfe von Boroskopen – von innen inspiziert, um nachvollziehen zu können, wie sich die einzelnen Komponenten durch die Belastung verändern. Anschließend wurde der Demonstrator in seine Einzelteile zerlegt und intensiv untersucht, um eventuell entstandene Risse oder andere Schäden zu identifizieren.
„Ziel eines solchen Tests ist es natürlich auch, zu lernen, was noch nicht wie gewünscht funktioniert und was folglich noch weiterentwickelt werden muss“, sagt Wulf. Denn die Arbeit ist mit der Auswertung der Testdaten für MTU nicht beendet. Auch im Rahmen des Nachfolgeprogramms Clean Sky 2, das seit 2014 und bis 2020 läuft, werden weitere Technologien entwickelt, um das ehrgeizige Ziel einer Treibstoffreduzierung um bis zu zehn Prozentpunkte im Vergleich zum heutigen Getriebefan zu erreichen. Zur Erprobung sollen wieder Demonstratoren dienen, die zwischen 2017 und 2020 getestet werden könnten.
Wann genau die mit SAGE 4 erprobten Technologien in Serientriebwerken eingeführt werden, steht noch nicht fest. Die neuen Materialien, Bauweisen und Designs sollen aber unmittelbar in die nächste Generation von Getriebefan-Triebwerken einfließen, heißt es bei MTU. „Wir sprechen hier von Antrieben, die bereits im Laufe des kommenden Jahrzehnts fliegen könnten“, sagt Henne.
Forschungsprogramm Clean Sky
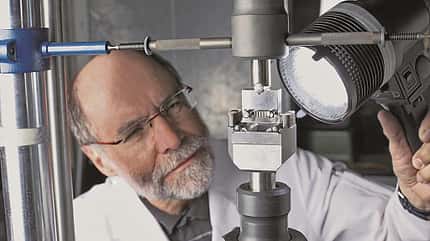
Clean Sky
Clean Sky ist ein Gemeinschaftsvorhaben der EU-Kommission und der europäischen Luftfahrtindustrie. Die öffentlich-private Partnerschaft koordiniert und fördert die Forschung an Zukunftstechnologien, die Flugzeuge leiser und umweltfreundlicher machen sollen. Die Initiative Clean Sky 1 startete 2008 und läuft Ende 2016 aus. Ausgestattet mit einem Budget von 1,6 Milliarden Euro, sollte Clean Sky 1 dabei helfen, zunächst die Ziele des Advisory Council for Aeronautics Research in Europe (ACARE 2020) und ab 2011 der Strategie Flightpath 2050 zu erreichen. Dazu gehören eine Reduzierung der CO2-Emissionen um 75 Prozent, eine Senkung des Stickoxidausstoßes um 90 Prozent und eine Lärmverringerung um 65 Prozent im Vergleich zum Jahr 2000. 2014 begann das Nachfolgeprogramm Clean Sky 2, das noch bis 2020 dauert. Vier Milliarden Euro stehen dafür zur Verfügung.
PW1500G Daten
PW1519G | PW1521G | PW1524G | PW1525G* | |
Bläserdurchmesser | 185,42 cm | |||
Architektur | Bläser, Getriebe, Niederdruckverdichter (3 Stufen), Hochdruck- verdichter (8), Hochdruckturbine (2), Niederdruckturbine (3) | |||
Startschub | 84,5 kN | 93,4 kN | 103,6 kN | 103,6 kN |
Nebenstromverhältnis | 12:1 | |||
Flugzeug | Bombardier CS100 | Bombardier CS100, CS300 |
*liefert unter bestimmten Bedingungen bis zu fünf Prozent mehr Schub
FLUG REVUE Ausgabe 01/2017