Am Boden tragen sie die ganze Last eines Flugzeugs und bei einer Landung müssen sie zuweilen harte Stöße abfangen: Fahrwerke sind wahre Schwerstarbeiter in der Luftfahrt. Damit sie den enormen Belas- tungen standhalten, werden sie im Fahrwerkslabor von Liebherr-Aerospace Lindenberg ausgiebig geprüft. Und zwar sowohl während der Entwicklung als auch später bei der Zulassung.
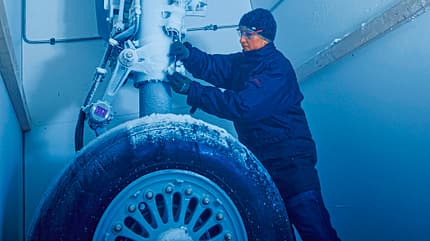
Weltweiter Kundenkreis
Das Fahrwerkslabor ist Teil des insgesamt 8500 Quadratmeter großen Qualifikations- und Testzentrums des deutschen Luftfahrtzulieferers. Der Betrieb wurde 2003 aufgenommen, heute sind dort rund 145 Frauen und Männer beschäftigt. Allein im Rahmen der Serien- und Reparaturlieferungen durchlaufen jährlich etwa 5000 Fahrwerke und Komponenten Abnahmetests. "In Deutschland sind wir der größte Anbieter für integrierte Test- und Qualifikationsleistungen für Fahrwerkssysteme und Flugsteuerungen", sagt Harry Brülke, der Leiter des Qualifikations- und Testzentrums.
Zu den Kunden gehören unter anderem Airbus, Boeing, COMAC und Embraer (siehe Kasten rechts). Getestet werden einzelne Komponenten, aber auch ganze Systeme: vom Cockpit über die elektrische und hydraulische Ansteuerung der verschiedenen Betätigungsventile und -zylinder bis hin zu Bug- und Hauptfahrwerken. "Generell ist es so, dass unsere Tests hauptsächlich die Flugzeugprogramme betreffen, die sich in der Entwicklungsphase befinden", so Brülke. Aber selbst für Flugzeuge, die bereits im Liniendienst stehen, gehen die Langzeittests im Labor oft noch ein bis zwei Jahre lang weiter.
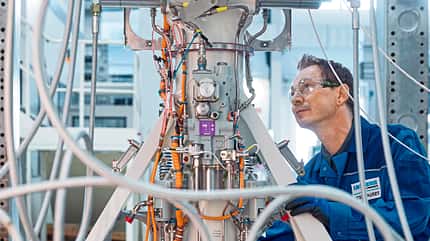
Maßgeschneiderte Anlagen für Extremtests
Die Prüfstände werden von Liebherr-Aerospace selbst entwickelt, gebaut und gewartet. Möglichst modulare Konstruktionen sorgen dafür, dass verschiedene Fahrwerke getestet werden können. Im System-Testrig kann beispielsweise das komplette Fahrwerkssystem inklusive Bremsen und Rädern erprobt werden – unter normalen Bedingungen, bei Temperaturen von -60 bis +85 Grad Celsius, bei Vereisung mit Schichtdicken von drei bis 13 Millimetern, bei einer Luftfeuchtigkeit bis 95 Prozent und bei Luftdrücken, die einer Höhe von 51 000 Fuß (15 545 Metern) entsprechen. Im Prüfstand für Belastungs- und Ermüdungstests erfassen Kameras anhand von auf dem Fahrwerk aufgebrachten Punkten die Deformation unter verschiedenen Lasten. Selbst Windlasten auf die Fahrwerksklappen können simuliert werden. Liebherr-Aerospace hat sogar einen Prüfstand entwickelt, mit dessen Hilfe die Stöße auf schlechten Landebahnen nachgestellt werden können.
Bevor Fahrwerke an einem Flugzeug zum Einsatz kommen, müssen sie diverse Qualifikationstests in Lindenberg bestehen. Wichtig ist dabei zunächst die sogenannte Safety of Flight (SoF, Flugsicherheit). Dabei geht es darum, maximale Betriebslasten sowie Funktionen und Leistungen des Fahrwerks nachzuweisen, damit es für die Flugtestphase genutzt werden kann. Im Rahmen dieser SoF-Tests werden die Fahrwerke, zum Teil auch in Zusammenarbeit mit ausgewählten externen Laboren, unter anderem auf Vibrationen und ihre elektromagnetische Verträglichkeit untersucht.
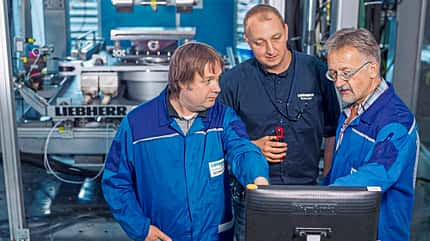
Auch Zertifizierungstests für die Freigabe in der zivilen Luftfahrt finden bei Liebherr-Aerospace statt. Im Rahmen dieser Kampagnen müssen Fahrwerke beispielsweise dem 1,5-Fachen der maximalen Betriebslast standhalten. Die Prüfingenieure gehen aber auch über die Grenzen hinaus und belasten das Fahrwerk, bis es bricht. Solche Bruchtests sind Teil der Entwicklung und Qualifikation. Der größte Teststand in Lindenberg kann durch Aktuatoren etwa 300 Tonnen Druck ausüben.
Auch bei Hitze und Staub funktionsfähig
Bei sogenannten Umwelttests müssen die Fahrwerke für die Zulassung beispielsweise auch bei extremen Tempe-raturen und Luftdrücken sowie bei Sand und Staub ihre Funktionsfähigkeit beweisen. Die Strukturkomponenten seien aufgrund ihrer ausfallsicheren Konstruktion unkritisch. Die empfindlichsten Teile eines Fahrwerks, vor allem die Sensorik und exponierte Anbauteile inklusive Kabel, seien aber unter anderem durch Vogelschlag und Hagel gefährdet und müssten zeigen, dass sie robust genug sind. "Jedoch sind zur Sicherheit alle kritischen Systeme wie zum Beispiel Bremsen immer redundant ausgelegt", sagt Brülke. Selbst nach einem Ausfall einzelner Komponenten könne immer noch sicher geflogen, gelandet und gebremst werden.
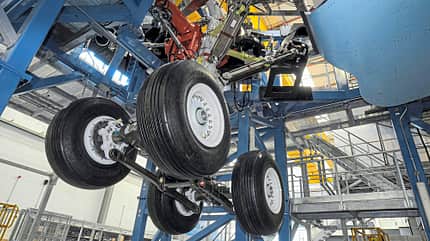
Der Hersteller muss für die Zulassung zudem Nachweise über das Verschleiß- und Ermüdungsverhalten erbringen. Für jedes Fahrwerkssystem werden nach Angaben von Liebherr- Aerospace 150 bis 200 Qualifikationstests durchgeführt. Daneben werden in Lindenberg auch Entwicklungstests und Versuche an Prototypen sowie zur Grundlagenforschung durchgeführt. Ein Beispiel ist der Prototyp eines elektrischen Aktuators für ein Hubschrauberfahrwerk, in dem Motor, Zahnradantrieb und Energieversorgung in einer Einheit gebündelt sind.
FahrwerksInnovationen im Labortest
Vor einigen Jahren hat Liebherr-Aerospace auch schon ein Fahrwerk aus Kohlefaser untersucht. Es ist zwar leichter und bewies in den Tests dieselbe Festigkeit wie ein Fahrwerk aus Stahl, doch wegen noch bestehender Herausforderungen im echten Airline-Betrieb haben sich solche Systeme bisher nicht durchgesetzt. Aber wer weiß, vielleicht durchlaufen sie ja eines Tages auch die Qualifikationstests in Lindenberg.
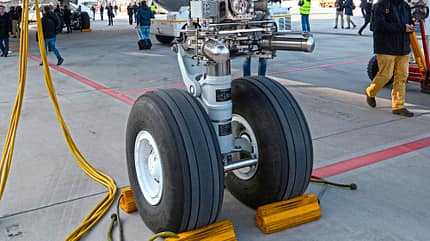
Fahrwerke und Fahrwerkskomponenten von Liebherr Aerospace
Airbus
A220: Fahrwerkssystem
A300-600: Bugfahrwerk, Fahrwerksklappen- Betätigungszylinder
A310: Bugfahrwerk
A350 XWB: Bugfahrwerk
Airbus Defence & Space
Eurofighter Typhoon: Bugfahrwerk und Einfahr-Betätigungszylinder, Hauptfahrwerk-Seitenstreben
Airbus Helicopters
Tiger: Heckfahrwerk
Boeing
Boeing 777/777X: Hauptfahrwerksteuerungssystem
Boeing 787: Elektronische Bugradlenkung-Steuereinheit
MH-139: Fahrwerkssystem
Bombardier
Global Express: Dämpferstrebe Bugfahrwerk
G5000/G5500: Dämpferstrebe Bugfahrwerk
COMAC
ARJ21: Fahrwerkssystem inklusive Bremssystem, Räder und Reifen
C919: Fahrwerkssystem
Embraer
E-Jets: Fahrwerkssystem inklusive Bremssystem, Räder und Reifen
E2-Jets: Bugfahrwerk-Lenkungsmodul
Embraer 135/145/Legacy 650: Bugfahrwerk
Lineage: Fahrwerkssystem inklusive Bremssystem, Räder und Reifen
FAdeA
IA-63 Pampa III: Fahrwerkskomponenten
HAL
Dornier 228: Bugfahrwerklenkungssystem, Fahrwerksbetätigungs-zylinder
Leonardo
AW139/149/189: Fahrwerkssystem
M-346: Bugfahrwerklenkungssystem, Bugfahrwerkssystem, Hauptfahrwerkssystem
RUAG Aerospace
Dornier 228 New Generation: Bugfahrwerklenkungssystem, Fahrwerksbetätigungs-zylinder