Henning Scheel drückt auf den Start-Button des Programms auf seinem Computer. Aus hunderten Lautsprechern ertönt ein Sound wie aus einer Bassgitarre, tief, durchdringend, aber es mischen sich auch höhere Frequenzen hinein. "Das entspricht in etwa dem Lärmpegel des Counter Rotating Open Rotor", sagt Scheel. Er ist Leiter des Acoustic Flight Lab von Airbus im ZAL TechCenter in Hamburg. Dort wird mithilfe eines freischwingenden Kabinendemonstrators mit dem Durchmesser eines Airbus-A320-Rumpfs erforscht, wie sich Lärm und Vibrationen in der Flugzeugstruktur ausbreiten und wie man damit umgehen kann. "Es geht nicht nur um Lärmreduzierung, sondern auch darum, wie man Geräusche besser klingen lassen kann", sagt Scheel.
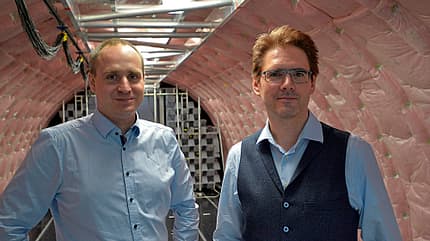
Lärm wie auf der Autobahn
Vom ausgefeilten Sounddesign der Autoindustrie, wo das Geräusch jedes Türschlags beeinflusst wird, ist die Luftfahrt zwar noch weit entfernt. Dennoch beschäftigt sich Airbus schon seit Jahrzehnten mit der Kabinenakustik. "Für uns ist das ein Alleinstellungsmerkmal, das wir weiter vorantreiben wollen", sagt Scheel. Der Schwerpunkt der Kabinenakustikforschung liegt in Hamburg, wo rund 30 Mitarbeiter mit dem Thema beschäftigt sind. Neben dem Akustiklabor im ZAL, dessen exklusiver Mieter Airbus bis 2021 ist, verfügt der Flugzeughersteller im Werk nebenan in Finkenwerder über ein eigenes Akustikzentrum. Kein Wunder, dass die aktuell leiseste Flugzeugkabine diejenige der A380 ist. Das sagt nicht Airbus selbst, sondern Dr. Kay Kochan vom Center of Competence Cabin & Systems des ZAL: "In der Akustik gilt das sogenannte Massegesetz der Luftschalldämmung – es besagt, dass die Luftschalldämmung mit sechs Dezibel pro Masseverdopplung steigt."
Hauptquellen für Lärm
Die Hauptquellen für Lärm in der Kabine sind neben den Triebwerken das Fahrwerk, die Hochauftriebssysteme, der Umströmungslärm am Rumpf, aber auch die Klimaanlage und das Hydrauliksystem. "Der Kabinenlärm ist ein breitbandiges Rauschen mit tonalen Anteilen. Das Maximum des A-bewerteten Spektrums liegt bei etwa 400 bis 1000 Hertz und ist abhängig vom Flugzeug, Flugzustand und dem Ort in der Kabine", sagt Dr. Kochan. Die Plätze, die Passagiere als am ruhigsten empfinden, seien diejenigen vor den Flügeln, weit entfernt von Bordküchen und Toiletten. Und selbst das Wetter hat einen Einfluss darauf, wie laut es in der Kabine ist: Zehn Grad Temperaturunterschied entsprechen etwa einem bis zwei Dezibel – je wärmer, desto leiser. Im Schnitt liegt der Geräuschpegel heutiger Kabinen im Reiseflug zwischen 75 und 80 dB(A). Das ist vergleichbar mit dem Lärm einer stark befahrenen Autobahn.
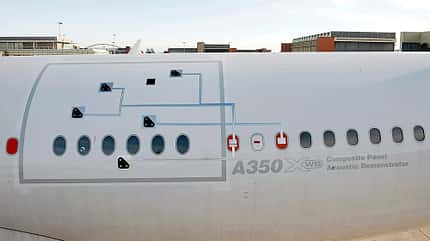
Unterschiedliche Ansätze
Um die Kabinenakustik zu beeinflussen, gibt es unterschiedliche Ansätze. Zum einen wird an den Lärmquellen selbst gearbeitet, also an Triebwerken und anderen Systemen. Beispielsweise sind moderne Turbofans unter anderem wegen des zunehmenden Nebenstromverhältnisses leiser als frühere Antriebsgenerationen. Zum anderen gibt es die sehr aufwendige und teure Umsetzung von Antischall-Konzepten. Dabei wird eine Schallwelle von einer gegenläufigen Schallwelle überlagert und eliminiert. Bombardier nutzt ein solches System, das Mikrofone, ein Regelsystem und Aktuatoren umfasst, beispielsweise in der Kabine des Turboprop-Flugzeugs Q400. Auch Airbus hat sich schon mit Antischall beschäftigt, Kosten und Nutzen stünden aber für Jets in keinem Verhältnis. "Bei der Active Noise Control arbeiten wir mit anderen Industriepartnern zusammen, da dies derzeit eher ein Thema für Inflight-Entertainment-Systeme oder Premium-Sitz-Hersteller ist", sagt Dr. Kochan.
Neue Materialien im Fokus
Eine weitere Möglichkeit für leisere Kabinen sind Strukturmaßnahmen wie eine Schalldämmung zwischen Rumpfaußenhaut und Kabinenseitenwand. Bislang kommen thermoakustische Isolierungen beispielsweise aus Glaswolle zum Einsatz. Für eine künftig noch bessere Dämmung interessant sind sogenannte akustische Metamaterialien. "Es handelt sich dabei um geschickte Materialkombinationen mit kleinen resonanten Strukturen, die sich auf bestimmte Frequenzen einstellen lassen", erklärt Dr. Kochan. Diese Metamaterialien können aus Schäumen, Kunststoffen, Metallen, aber auch Naturfasern bestehen.
New Acoustic Insulation Meta-Material Technology for Aerospace
Akustische Metamaterialien stehen auch im Fokus des deutsch-kanadischen Forschungsvorhabens NAIMMTA (New Acoustic Insulation Meta-Material Technology for Aerospace). Geleitet wird es vom ZAL und dem Quebecer Unternehmen Mecanum, beteiligt sind unter anderem Airbus, der Isoliermaterial-Hersteller Hutchinson, aber auch die Hochschule für Angewandte Wissenschaften Hamburg. Im Rahmen des seit September 2017 laufenden, drei Jahre dauernden Projekts sollen neue Materialien auch im Acoustic Flight Lab im ZAL TechCenter untersucht werden.
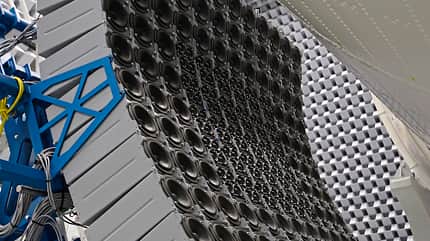
Die Zahl der individuell steuerbaren Lautsprecher liegt bei 444, aufgeteilt auf zwei Systeme, die auf einer Schiene um das Rumpfstück herum bewegt werden können. Durch die Kabine fährt gleichzeitig ein Mikrofonsystem, das den Lärm kartiert. Die leere, 8,5 Meter lange Röhre lässt sich komplett mit Sitzen, Galley und Seitenverkleidungen ausstatten.
Ziel sind weniger Flugtests
Im Akustiklabor sind laut Airbus reale Tests unter kontrollierten Bedingungen möglich. Das soll zum einen die Zahl der Flugversuche verringern, zum anderen aber auch die vibroakustische Simulation verbessern. "Bei der A350 gab es noch viele Testflüge, um zu untersuchen, welche Unterschiede sich durch Kohlefaserverbundwerkstoffe ergeben", sagt Scheel. Generell hätten CFK-Strukturen wegen des geringeren Gewichts und der höheren Steifigkeit gegenüber Aluminium den Nachteil, dass der Schalldurchgang höher sei, erklärt Dr. Kochan. Dennoch ist die A350-Kabine durch die neuen Rolls-Royce Trent XWB, geschickte strukturelle Maßnahmen und eine entsprechend angepasste Schallisolierung nach Angaben von Airbus bis zu viermal leiser als die der Boeing 787.
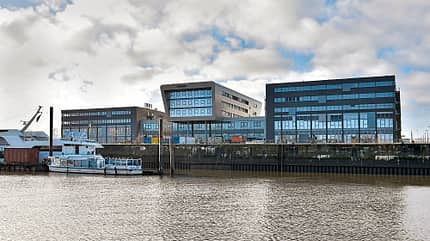
ZAL TechCenter in Hamburg
Das ZAL wurde 2009 als öffentlich-private Partnerschaft gegründet, um Hamburgs Position als drittwichtigsten zivilen Luftfahrtstandort nach Seattle und Toulouse zu festigen. Die größten der insgesamt neun Gesellschafter sind mit einem Anteil von jeweils 20 Prozent die Hansestadt Hamburg, Airbus sowie Lufthansa Technik. 18 Prozent hält der ZAL Förderverein, in dem sich Industrieverbände und Luftfahrtzulieferer zusammengeschlossen haben. Das Deutsche Zentrum für Luft- und Raumfahrt (DLR) ist mit zehn Prozent beteiligt, die vier Hamburger Hochschulen haben jeweils drei Prozent Anteil.
Anfang 2016 eröffnete das ZAL TechCenter in Hamburg-Finkenwerder. Auf mehr als 26 000 Quadratmetern Nutzfläche bietet es 600 Arbeitsplätze sowie Labore und Hangars. Im ZAL TechCenter sollen etablierte Unternehmen, Startups und Hochschulen gemeinsam an Innovationen arbeiten und neue Produkte schneller zur Marktreife führen.
Das ZAL legt den Fokus auf drei Themenfelder:
Flugzeugfertigung und Instandhaltung, Kabine und Systeme sowie Digitalisierung. In diesen Bereichen bietet es den Industriepartnern Forschungsdienstleistungen an. Zudem stellt das ZAL verschiedene Test-Infrastrukturen bereit, neben dem Akustiklabor sind das unter anderem ein Kabinen- und Frachtteststand, aber auch ein Laborfür Brennstoffzellen-Forschung.