Wild zuckt der Laser hin und her, aber es handelt sich nicht um eine Lightshow in der Diskothek oder eine Szene aus einem Science-Fiction-Film. Nach ein paar Sekunden ist das Schauspiel zu Ende, kurz ist der Umriss eines technischen Bauteils zu erkennen. Rechts hebt sich ein Pulverbehälter, ein Rakel verteilt feines Metallpulver über die Arbeitsfläche, und zwar mit einer Dicke von nur 20 bis 40 µ - ein µ entspricht einem tausendstel Millimeter. Sofort beginnt die Laserflamme wieder über die 25 mal 25 Zentimeter große Bauplattform zu zucken. Sie schmilzt das Pulver in der Form des ersten Schnittes eines Bauteils auf, das zuvor am Rechner in die entsprechenden Ebenen unterteilt wurde. Das Ganze findet in einer Argon-Schutzgasatmosphäre statt, um Oxidation weitgehend zu vermeiden. So entsteht dann in diesem Pulverbett Stück für Stück ein ganzes Bauteil, das anschließend nur noch per Drahterosion von der Platte geschnitten und derzeit noch wie ein Gussteil oberflächenveredelt werden muss. Aber selbst dieser Arbeitsschritt könnte in Zukunft entfallen. Die rund eine halbe Million Euro teure Anlage stammt von der nur wenige Kilometer von München entfernten Firma Electro Optical Systems.
Der neueste Stolz von MTU Aero Engines nennt sich „generatives Verfahren“ und könnte in den nächsten Jahren den Triebwerkskonstrukteuren zu ungeahnten Möglichkeiten verhelfen. „Wir bauen seit Jahrzehnten nicht anders, nur mit Guss, nur mit Vollmaterial, aus dem herausgefräst wird. Jetzt fangen wir wirklich an, ein Bauteil geometrienah aufzubauen, in das schon vieles integriert ist“, sagt Dr.-Ing. Andreas Jakimov, bei der MTU unter anderem verantwortlich für die Verfahrensentwicklung. Ein großer Vorteil liegt dabei in der Reduzierung des Gewichts, denn bisher ausgefüllte Strukturen könnten nun hohl und mit inneren Gitterstrukturen ausgelegt werden, und das bei nahezu identischen Festigkeiten. „Nach unseren Rechnungen kommen wir auf Werte von 90 Prozent der Festigkeit eines Vollmaterials bei ungefähr 40 Prozent Gewichtserleichterung.“ Außerdem lassen sich Designänderungen relativ schnell durchführen und die Entwicklungszeit deutlich verkürzen. „Beim Guss dauert es bis zu einem halben Jahr, bis man das Bauteil testen kann. Hier kann der Konstrukteur im CAD etwas verändern, und zwei Wochen später hat er das Teil auf dem Tisch.“
Die Anwendungsmöglichkeiten sind sehr breit: Etwa können Turbinenleitschaufeln samt ihren Honigwabendichtungen mit nur millimetergroßen Öffnungen direkt aus einem Stück aufgebaut werden. Selbst ein aus einem Stück bestehendes Kugelgelenk ist schon entstanden, indem die Ingenieure einfach zwischen zwei Segmenten ein paar µm Platz ließen. Das Verfahren eignet sich aber heute prinzipiell nur für alle schweißbaren Materialien. Einige Gussteile lassen sich nicht derart aufbauen, weil der hohe Temperaturgradient - die Umgebung in der Maschine hat nahezu Raumtemperatur, der Schweißpunkt ist aber mit mehr als 2000 Grad sehr heiß – bei bestimmten Materialien zu Rissen führen kann. Eine weitere Herausforderung stellen die benötigten Stückzahlen dar, denn zur Erhöhung der Produktivität müssen die Maschinen schneller arbeiten. Derzeit dauert die Fertigstellung eines Teils 24 bis 48 Stunden, bei größeren Komponenten (derzeit ist eine Höhe bis 25 cm möglich) bis zu einer Woche. Dies könnten beispielsweise zusätzliche Laser beschleunigen. Außerdem müssen die Konstrukteure genau überlegen, wie sie das Teil ausrichten und platzieren, da keine Überhänge möglich sind und sie daher Stützstrukturen anbauen müssen, um sie später wieder wegzuschneiden.
Geänderte Rahmenbedingungen
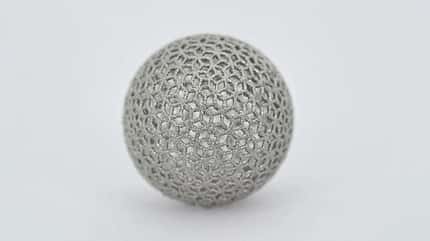
Viel zu tun haben Jakimov und sein Team auch auf dem Gebiet der Werkstoffkunde: „Mit dem Verfahren bearbeiten wir zwar Werkstoffe, die chemisch dieselben sind, nur das Herstellverfahren verändert sie insofern, als dass ganz neue Eigenschaften herauskommen. Man muss den Werkstoff komplett neu zulassen, das ist sehr umfangreich. Auch dieses Verfahren an sich muss für die Luftfahrt zugelassen werden.“ Dabei arbeitet die MTU unter anderem eng mit der TU München zusammen.
Trotz aller Fortschritte wird sich die Fertigung von Antrieben nicht komplett verändern. „Grob geschätzt bleiben 80 Prozent in der Triebwerksproduktion prinzipiell gleich. Immer mal wieder kommt es aber zu Innovationsschüben. Solche Schübe bringt etwa jede neue Triebwerksgeneration mit sich“, sagt Richard Maier, Leiter Produktionsentwicklung und Support bei der MTU. „Seit über 35 Jahren besteht eine Turbinenscheibe aus einer Nickelbasislegierung und wird von uns gedreht, geräumt, gefräst, gebohrt, entgratet und gewaschen. Diese Grundprozesse sind nach wie vor die gleichen, wir arbeiten heute aber integrativer; d.h. Bearbeitungsverfahren werden auf einer Maschine kombiniert und die Maschinen sind deutlich produktiver. Auch die eingesetzten Schneidwerkstoffe sind wesentlich besser als früher. Das zusammen macht uns schneller und letztendlich auch wirtschaftlicher in der Produktion von Triebwerksteilen.“
Gleichzeitig haben sich gerade in den letzten Jahren die Rahmenbedingungen nicht nur bei der MTU verändert. Während die militärischen Programme weniger werden, steigt der Auftragseingang aus dem zivilen Markt enorm. So müssen viele neue Verfahren bereits in der zivilen Welt industrialisiert werden, und das bei kürzeren Entwicklungszeiten. Zudem müssen die Fertigungsspezialisten aufgrund kontinuierlicher Produktverbesserungsprogramme (PIP) immer mit Optimierungsveränderungen am Produkt rechnen.
Herausforderung hohe Stückzahlen
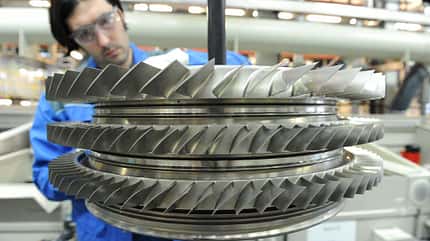
Aktuelle Herausforderungen müssen die Triebwerksfirmen dabei besonders in der Blisk-Fertigung bewältigen. In Oberursel produziert Rolls-Royce Deutschland beispielsweise drei Verdichter-Blisk-Stufen aus einer Nickellegierung für das Trent XWB. Laut Dr. Thomas Haubold, der als Manager Capability Acquisition für die Technologieentwicklung in Oberursel verantwortlich ist, muss die Produktion um 20 bis 30 Prozent pro Jahr erhöht werden. „Wir optimieren die Prozesskette, um schneller arbeiten zu können, die Kapazitäten der Maschinen besser zu nutzen und die Rüstzeiten zu minimieren.“ Obwohl sich der hitzebeständigere Werkstoff Nickel schwerer bearbeiten lässt als Titan, setzt Rolls-Royce auf das Zerspanen: „Fräsen hat die Nase vorn, beim elektrochemischen Abtragen sind noch einige technische und wirtschaftliche Fragen zu lösen.“
Die Verwendung einer neuen Fertigungstechnik hängt indes nicht nur von der Technologie ab, sondern wird auch von der Wirtschaftlichkeit bestimmt. Angesichts der kürzeren Entwicklungszeiten tritt auch der Bereich Simulation laut Dr. Haubold von Rolls-Royce Deutschland immer mehr in den Vordergrund. „Aufgrund der engen Zeitpläne gibt es nur wenige Probeteile bis zum Test im Triebwerk. Die Teile müssen von Anfang an schon sehr nah an den Anforderungen sein. Der Wunsch ist, den Weg von einem Schmiedeteil bis hin zum fertigen Bauteil zu simulieren.“ Die Ingenieure hoffen, in Zukunft die Ergebnisse eines Bearbeitungsprozesses für eine Komponente, etwa das Aufbringen von Eigenspannung durch Drehen, berechnen zu können. Die Erkenntnisse geben sie dann an die Festigkeitsabteilung weiter. Früher waren dazu ausgiebige Hardware-Versuche nötig. Allerdings sind für die Simulation ausgefeilte Rechenmodelle nötig, an denen die Hersteller gerade arbeiten.
FLUG REVUE Ausgabe 01/2012