Airbus-Finkenwerder. Jeden Monat spucken alleine die drei Hamburger A320-Endmontagelinien gut 30 neue Flugzeuge aus. Und die Rate wird weiter erhöht: Konzernweit will Airbus bis Mitte 2019 pro Monat 60 Flugzeuge seiner Standardrumpf-Familie bauen – derzeit sind es rund 50 im selben Zeitraum. Eine vierte A320-Linie in Finkenwerder soll dabei helfen und die Rate perspektivisch gar auf 70 Flugzeuge im Monat erhöhen.
Hinzu kommt in Hamburg der Airbus A380, der hier, neben der Sektionsmontage, innen ausgestattet und lackiert wird und von dem Exemplare für europäische und nahöstliche Kunden, darunter Emirates, gleich ab der Elbestadt ausgeliefert werden. Hamburg überholte 2016 sogar Toulouse nach gebauter Stückzahl. Doch bevor die neuen Hightech-Geräte beim Kunden landen, beginnt ein mehrteiliges Abnahmeverfahren, mit dem ganze Spezialabteilungen betraut sind. Carlos Alcántara, er trägt den Titel „Head of Acceptance & Delivery, A320 Family Final Assembly Line Hamburg”, holt jede Hamburger A320 oder A321 mit seinen Leuten von der Endmontage ab. Der Fluggerätmechaniker mit spanischen Wurzeln und norddeutschem Akzent lernte den Flugzeugbau von der Pike auf und begann schon mit 15 Jahren in Finkenwerder seine Lehre. Er nennt sich selbst penibel, sensibel und perfektionistisch. “Wir übernehmen das Flugzeug nach dem Final Operational Test von der Endmontage. Das bedeutet, das Flugzeug ist komplett fertig und kann fliegen„, erläutert er die Zusammenarbeit mit der Produktionsabteilung.
Werkstattflüge mit allen Schikanen
Noch bevor der Kunde ins Spiel kommt, prüft Alcántara das neue Flugzeug aber erst noch einmal in allen Details und bringt den nagelneuen Jet zum “Flightline„-Flugbetriebsvorfeld. Hier erfolgen Boden- und Systemtests, gefolgt von Triebwerksstandläufen. Dann wird es ernst, der neue Zweistrahler startet zum Erstflug. Zwei Airbus-Testpiloten, gleich beide im Kapitänsrang, außerdem ein Flight Test Engineer und noch ein Testingenieur in der Kabine bereiten den Jet mit zwei Startabbruchtests, einem mit Schubumkehr und einem nur mit Radbremsen, auf den Start vor.
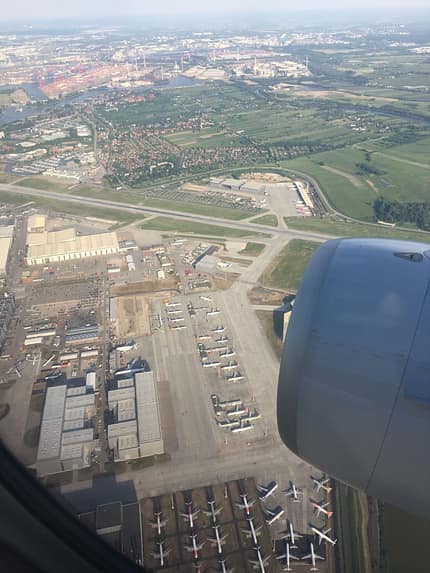
Dann beginnt ein genau geplanter Flug, der in immer gleicher Folge als Standardflugprofil alle Systeme und Anzeigen schrittweise und methodisch in der Luft prüft. Jeder neue Airbus wird im gesamten Funktionsbereich bewegt, und alle Anzeigen, Warnanzeigen und Reservesysteme werden aktiviert, geprüft und gegebenenfalls feinjustiert. “Wir fliegen ausschließlich innerhalb des Flight Envelopes, das ist nicht wie bei einem Testflug mit einem völlig neuen Muster„, stellt Thomas Heidemann klar. Der an der Testpilotenschule im südfranzösischen Istres zum Flugtestingenieur weitergebildete Ingenieur ist zusätzlich ATPL-Linienpilot und wechselt sich bei den Abnahmeflügen häufig mit seinen Kollegen am Steuer ab. Als Flight Test Engineer trägt er jedoch die Gesamtverantwortung. Nach dem Abheben geht es, das erste Stück per Autopilot, in einen von zwei speziellen Lufträumen, welche die Deutsche Flugsicherung den Testflügen jeweils nach Verkehrslage zuweist – entweder über die Nordsee bis etwa Helgoland oder über Nordostdeutschland und Rügen. Dabei betreut ein persönlicher DFS-Fluglotse jeweils einen gesamten Testflug und hält diesem nach Absprache “den Rücken frei„.
Für Leistungsmessungen oder die Feinjustierung der Steuerung muss man oft minutenlang genau gegen den Wind oder mit dem Wind fliegen oder spezielle Manöver oder wechselnde Steig- und Sinkflüge durchführen, sodass dem Testflug ein Luftraum oft als ganzer Block zugewiesen wird. Am Radar sieht der Flugverlauf oft wie eine wirre Folge von rennbahnartigen Ovalen mit Kehrtwenden aus. Aber alle Manöver folgen einer systematischen, genau so erforderlichen Reihenfolge.
Mit dem Airbus auf Cessna-Tempo
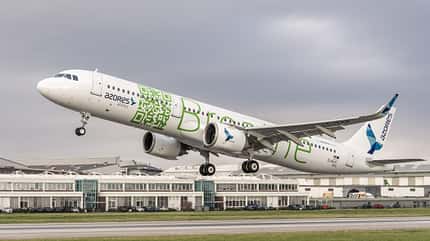
In Cockpit und Kabine herrscht derweil Testroutine. Die Besatzung arbeitet Schritt für Schritt ihre Aufgaben ab. Im Flug werden zum Beispiel in der Kabine Windgeräusche oder Zugluft an den Kabinentüren geprüft. Auch darf es keinesfalls nach schmorenden Leitungen oder heißer Elektrik riechen. Alle Schranktüren, Gepäckfächer oder andere Luken in der Kabine werden bei erhöhtem Kabinendruck im Flug bewegt, da sie sich gegenüber der Lage am Boden verzogen haben und plötzlich quietschen oder knarzen könnten. Alle Messungen werden protokolliert. Für Druckkabinenproben und Geschwindigkeitstests klettert die A320 von Flugfläche 310 bis auf Flugfläche 390 (11.900 Meter), wobei nun die “Leckrate„ bei abgeschalteter Versorgung gemessen wird. Schließlich beschleunigt der Jet auf Mach 0.78. Nach eine Reihe von Leistungsmessungen geht es wieder “bergab„, mit Tests der Druckregelung, Sauerstoffmasken, mit Anlasstests der Hilfsgasturbine und einer auf Schwerkraft umgestellten Tankspeisung. Testingenieur Heidemann kann seinen Laptop an das Bordnetz anschließen, um gezielt Systemzustände abzufragen und zu speichern. Ein eigener Prüfungsbereich sind die Cockpitanzeigen. Auf den Knoten genau muss die Geschwindigkeitsanzeige ihre gelben und roten Warnbalken einblenden, ebenso auf den Punkt genau müssen die eingebauten Schutzmechanismen ansprechen. Etwa ein automatischer Vollgasbefehl, wenn das Flugzeug gefährlich langsam wird, nahe an die Mindestfahrt kommt, aber wirklich erst genau dann, nicht leicht vorher. Für die Hamburger Abnahmeflieger sind extreme Jet-Langsamflüge unter 100 Knoten (185 km/h) deshalb Alltag. Thomas Heidemann schwärmt von der Steuerbarkeit derA321neo auch bei Cessna-Tempo. Er schaltet zu Prüfungszwecken zeitweise absichtlich alle Hilfssysteme wie den Gierdämpfer ab und kann seine Zweistrahler selbst in dünnster Höhenluft präzise, wie eben nur ein Testpilot, rein manuell steuern.
“Überraschungen sind immer möglich„
Absichtlich nur mit Schwerkraft fährt der neue Jet, nun wieder unterhalb von 15.000 Fuß (4570 Meter) unterwegs, sein Fahrwerk aus und mittels Hydraulik wieder ein und provoziert dann mit einem steilen Sinkflug ein Ansprechen der automatischen Warnansagen für Bodenannäherung und Landeanflüge mit eingefahrenem Fahrwerk. Alle Warnlampen und Störanzeigen, die im späteren Flugbetrieb aufleuchten könnten, werden durch entsprechende Manöver und Schaltungen ausgelöst, damit jedes einzelne Flugzeug exakt wie in der Betriebsanleitung beschrieben funktioniert. Schwere Störungen sind selten. Alle Probeflüge werden mit äußerster Konzentration absolviert. “Überraschungen sind immer möglich„, sagt Thomas Heidemann nüchtern. So hatte er einmal mit dem plötzlichen Ausfall der Staudruckturbine für den Notstrom zu kämpfen, die er mit dazu absichtlich abgeschalteten Generatoren prüfte. Bei anderer Gelegenheit wurde die Flugzeugnase durch Hagel beschädigt, den das in einem bestimmten Modus eingestellte Wetterradar bei einer komplexen Wetterlage nicht korrekt angezeigt hatte. Heidemann konnte die technischen Ursachen beider Störungen herausfinden und abstellen. Danach wurde die gesamte Serie verbessert.
Abnahmeverfahren gipfelt im Eigentümerwechsel
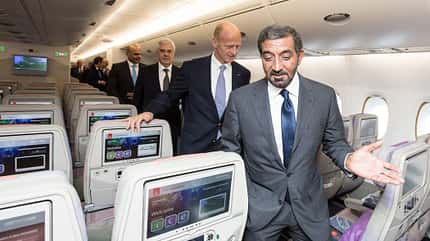
Nach dem Erstflug und dem Beheben aller “Findings„, wie man die Abweichungen nennt, seitens Airbus beginnt der Kunde seine eigene Endabnahme. Drei bis fünf Tage dauert diese bei einer A320. Manchmal kommen ganze Delegationen von 30 Mann Stärke, manchmal sind es nur ein oder zwei Experten, die zugleich auch viel Papierkram erledigen müssen, und manchmal überträgt der Kunde die kompletten Übernahmeformalitäten an Treuhänder oder direkt an Airbus. Mindestens ein nochmaliger Vorführflug mit dem Kunden präsentiert dessen Vertretern das nun praktisch perfekte Flugzeug.
Alles muss stimmen
Bis zu zwölf Kundenflüge können an einem typischen Tag in Finkenwerder stattfinden. Etwaige Mängel aus Kundensicht werden protokolliert und behoben. Am Ende muss der Jet von der heimatlichen Luftfahrtbehörde des Kunden zugelassen werden. Deswegen muss seine Ausstattung strikt deren jeweiligen Vorgaben entsprechen. Dann sind zum Beispiel Notausgangsschilder in exotischen Landessprachen und Alphabeten gefragt, spezielle Polar-Notausrüstungen oder übergroße Rettungsflöße an Bord oder eine ganz bestimmte Zusatzanmerkung in der Bedienungsanleitung vonnöten. Hier kommt wieder Carlos Alcántara ins Spiel. Seine Leute lassen notfalls auch per Taxi aus Toulouse ein benötigtes Teil holen, bevor ihnen die Zeit wegläuft. Die Airline-Mitarbeiter oder Leasingfirmen bestätigen mit ihrer Unterschrift die Freigabe der letzten Zahlung, was Transaktionen in Höhe von 60 bis 70 Millionen Euro bedeuten kann. Die Konformität mit allen behördlichen Vorgaben bescheinigt das abschließende Zertifikat “Form 52„. Nach der Übertragung des Eigentümerrechts, dem “Transfer of Title„, gehört der Jet dem Kunden, der Aufkleber über der endgültigen Registrierung wird abgezogen. Nun parkt das Flugzeug bis zum Überführungsflug auf einem isolierten Teil des Vorfelds. Nur mit Kundenerlaubnis gehen dann noch Airbus-Mitarbeiter an Bord.
Bloß keine Spuren hinterlassen!
Natürlich gibt es Flugzeuge aus Hamburg, diewesentlich größer als die der A320-Familie sind, nämlich die A380. Diese ist das Spezialgebiet von Jörn Senkspiel, Head of FAL Customer Management Hamburg, A380 Final Assembly Line/ Delivery. “Der Kunde ist König aber mehr als 100 Prozent geht nicht„, sagt Senkspiel gelassen über die Abnahmephilosophie, die trotz permanenten Zeitdrucks viel Geduld und Kundenverständnis erfordert. 75 Prozent der Abnahmearbeiten bei der A380 beziehen sich mittlerweile auf deren immer komplexere Luxus-Innenausstattungen der Business und der First Class, sagt Senkspiel. Dazu gehören beispielsweise spektakuläre Betten, Duschen, Bars, Sessel mit komplizierter Massageautomatik und Kühlluftgebläsen sowie LED-Beleuchtung sogar in den Teppichen am Boden. Licht darf nicht an der falschen Stelle durchscheinen, deshalb kontrollieren die Abnahmeteams die Kabine ausdrücklich auchauf “Light Leaks„, wörtlich “Lichtlecks„. Auf den klavierlackartigen, verführerisch glänzenden Verkleidungen sieht man jeden Kratzer oder Fingerabdruck. Deshalb sind die Airbus-Abnahmetrupps, die nur mit Schutzpantoffeln an Bord gehen, geradezu militärisch darauf gedrillt, keinerlei Spuren ihrer Arbeit zu hinterlassen. Große Werkzeugkästen wurden abgeschafft. Nur noch das aktuell benötigte Werkzeug wird mitgeführt, um bloß keine Dellen oder Beulen zu erzeugen, die wieder repariert werden müssten. Bei Bedarf rücken Polierteams an und wienern alles zu voller Pracht oder tauschen defekte Teile aus.
650 Sitzmonitore, 600 Kilogramm Farbe
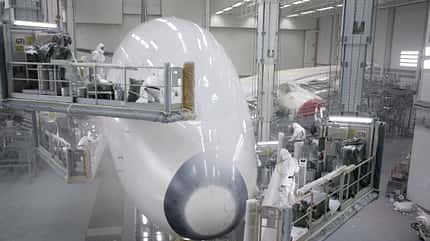
Auch bei der A380 gibt es noch Probe- und Abnahmeflüge:den technischen “Cabin First Flight„ nach Beendigung der in Hamburg vorgenommenen Einbauten, und wieder mehrere Flüge mit Kundenvertretern. Hier wird im Flug die gesamte Kabinenausstattung überprüft, zu der oftmals komplizierte Ausstattungsdetails und allerneueste Bordunterhaltungssysteme gehören. Bis zu 650 Sitzmonitore können in einer einzigen A380 installiert sein. Besonders genau werden die “Head of Versions„ unter die Lupe genommen, die ersten Vertreter einer Airline-Ausstattungsvariante, etwa mit neuem Design oder zusätzlicher Economy-Plus-Kabinenklasse.
Von den insgesamt rund 300 Neuflugzeugen – vor allem A320 –, die das Hamburger Auslieferungszentrum jährlich verlassen, sind etwa 120 Konfigurations-Erstlinge. Neun Tage dauert das übliche Abnahmeverfahren für die große A380. Am Boden umfahren die Kunden mit Hubbühnen ihren Jet, um die Lackierung auf Farbnasen oder Lackfehler abzusuchen. Immerhin 600 Kilogramm Farbe verteilen sich hier auf 3500 Quadratmeter Fläche.
Manchmal soll die Abnahme, selbst bei einer A380, auf Kundenwunsch heimlich stattfinden. Dann müssen technische Proben zu “unchristlichen„ Zeiten erfolgen, damit eine noch geheime Lackierung oder ein neues Logo nicht zu früh bekannt werden. Bei der jüngst vorgenommenen “Scheich Zayed„-Sonderlackierung von Emirates testete Airbus in Hamburg aus diesem Grund die Satellitenempfangsanlage mitten in der Nacht auf dem Vorfeld. Die Premiere gelang.
“Ein psychisches Erfolgserlebnis„
Monate vor der Abnahme richten die Kunden ständige Büros in den Abnahmetrakten ein und begleiten auch schon die Produktionsphase mit eigenen Experten und kritischem Blick. Jörn Senkspiel bereitet sich derzeit, gemeinsam mit seinen Toulouser Kollegen, schon auf die ANA-Abnahmemannschaft vor, die bald anrückt. Im Lauf der Zusammenarbeit bildet sich zwischen den Kundenvertretern und den Airbus-Partnern ein enges Verhältnis. “Man hat bei einer Abnahme sehr viel Stress, aber am Ende steht ein psychisches Erfolgserlebnis„, sagt Jörn Senkspiel zufrieden. Oft muss er unter Zeitdruck Experten im eigenen Haus konsultieren, die schleunigst noch benötigte Ersatzteile beschaffen und einbauen müssen und sei es nur eine neue Garderobentür. Deshalb gehört zum Anforderungsprofil der notfalls rund um die Uhr und feiertags arbeitenden Abnahmeteams und Kundenbetreuer viel diplomatisches Geschick, auch den eigenen Kollegen aus den Produktionsbereichen gegenüber, die selber nach engen, ganz anderen Taktplänen arbeiten. Wenn der Kunde am Dienstagmorgen nach Pfingsten sein neues Flugzeug abholen will, steht Jörn Senkspiel auch an einem Pfingstmontag oder nachts bereit.
neo-Nachholbedarf erhöht den Auslieferungsdruck
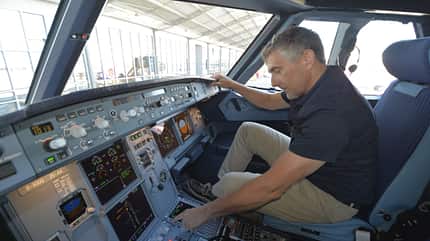
Während die Produktionsraten in Hamburg bei der A320-Familie immer weiter steigen, nehmen die Auslieferungen derzeit sogar noch schneller zu. Denn Airbus liefert nun auch schon fertig produzierte A320neo aus, die nun endlich mit modifizierten Triebwerken von Pratt & Whitney bestückt werden können. Noch parken an verschiedenen Konzernstandorten rund 100 der intern scherzhaft “Gleiter„ genannten neo-Flugzeuge ohne Triebwerke auf Halde, auch in Finkenwerder, eng gestellt auf allen verfügbaren Vorfeldern, und noch immer werden neue Stellflächen gebaut. Die lange Parkdauer einiger “Gleiter„ hat sogar zu Anpassungen bei den Abnahmearbeiten geführt. So werden die vorübergehend konserviert eingemotteten Jets vor der Übergabe nun zunächst blitzblank gewienert, sodass sie auch äußerlich wieder fabrikneu aussehen. Auch werden nur für die Standzeit extra beschaffte, gebrauchte Bremsen eingebaut, und erst zur Auslieferung an den Kunden erhält das Flugzeug seine fabrikneuen Original-Bremsen.