Schnell, leise, effizient: Haie sind mit ihrer Stromlinienform und ihrer außergewöhnlichen Schuppenstruktur ein perfektes Vorbild für die Luftfahrt. Denn wie im Wasser, so geht es auch in der Luft darum, den Reibungswiderstand zu verringern. Der Hai minimiert damit seinen Kraftaufwand beim Schwimmen, Flugzeuge potenziell ihren Kerosinverbrauch.
Schon seit Jahrzehnten inspirieren die feinen Rippen (Englisch: Riblets) der Haifischhaut auch die Luftfahrttechnik. Sie verringert Verwirbelungen, die auf der Oberfläche entstehen. Lufthansa Technik hat in Zusammenarbeit mit BASF kürzlich die „AEROShark“-Folie vorgestellt, die ab 2022 auf allen Boeing-777-Frachtern von Lufthansa Cargo zum Einsatz kommen soll. Doch auch im Triebwerksbau gibt es mögliche Anwendungen für das Prinzip.
Übergangskanal im Fokus der Forschenden
Ein Forscherteam der Technischen Universität Graz hat im vergangenen Jahr erstmals weltweit eine haifischhautähnliche Oberflächenbeschichtung im Übergangskanal zwischen Hoch- und Niederdruckturbine aerodynamisch erprobt. Das führte nachweislich zu einer Erhöhung des Wirkungsgrads. Die Arbeiten fanden im Rahmen des EU-Projekts TURANDOT (Turbulence and Duct Surface Optimization in Turbofans) statt, das von der österreichischen Forschungsförderungsgesellschaft (FFG) im "Beyond Europe"-Programm gefördert wurde. Geleitet wurde das Projekt vom Unternehmen Bionic Surface Technologies aus Graz. Beteiligt war auch der US-Triebwerkshersteller GE Aviation (mit den Standorten München, Cincinnati und Bangalore), der die Testgeometrie lieferte. Sie entsprach nach Angaben des Unternehmens einer Weiterentwicklung der State-of-the-Art-Übergangskanäle der neuesten Triebwerksgeneration, um einen möglichen Einsatz in zukünftigen Antrieben vorzubereiten.
Der Übergangskanal (auch Turbinenzwischengehäuse, Englisch: Turbine Center Frame) ist eine der Schlüsselkomponenten moderner Flugzeugtriebwerke. Denn je größer der Bläser, desto größer auch der Durchmesser der Niederdruckturbine, die ihn antreibt. Das bedingt einen kurzen und steilen Übergangskanal, der wiederum auch noch sehr hohe Temperaturen (rund 1000 Grad) aushalten muss. "Ein zu kurzer Übergangskanal könnte einen Strömungsabriss verursachen, da die Luft dem Strömungspfad aufgrund der aggressiveren Geometrie eventuell nicht mehr folgen kann", erklärt Emil Göttlich, Forscher am Institut für Thermische Turbomaschinen und Maschinendynamik der TU Graz. Die Folge: Druckverlust und reduzierte Triebwerksleistung.
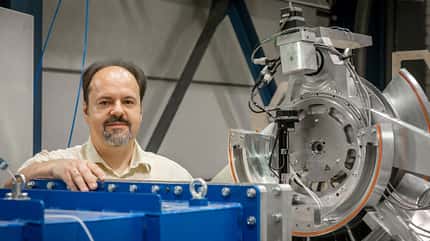
Dank der Riblet-Technologie konnte der Druckverlust nach Angaben der TU Graz unabhängig von der Geometrie um bis zu fünf Prozent reduziert werden. Für die Versuche nutzten die Forschenden selbstklebende Kunststofffolien, die von Bionic Surface Technologies entwickelt wurden. Die Tests fanden auf dem Hochgeschwindigkeits-Turbinenprüfstand im Turbomaschinenlabor der TU Graz statt, wo die Strömungsbedingungen real abgebildet werden können. "Die aerodynamische Ähnlichkeit wird vorwiegend über die Machzahl eingestellt und die thermische Ähnlichkeit über die korrekten Verhältniszahlen zwischen Kühllufttemperatur und jener der Hauptströmung", erklärt Göttlich. Dadurch ergäben sich repräsentative Versuchsbedingungen, allerdings nicht bei den hohen Temperaturen einer Gasturbine im echten Betrieb.
Künftige Triebwerke mit Haifischhaut-Beschichtung?
TURANDOT ist ein erster Schritt, die Haifischhaut-Technologie für Triebwerke zu erproben. Weitere Projekte beschäftigen sich nun damit, wie Riblet-Oberflächen auch für die hohen Triebwerkstemperaturen aufgebracht und über die gesamte Lebensdauer der Bauteile hinweg haltbar gemacht werden können.
Neben dem Übergangskanal könnten Riblets auch in anderen Triebwerkssektionen die Effizienz erhöhen. Grundsätzlich seien die Bereiche interessant, die eine möglichst große Oberfläche in der Strömung durch den Triebwerkskern oder die Bypass-Strömung beinhalten, so Göttlich. Als Beispiele nennt er Oberflächen stromab des Bläsers im Nebenstrom. Es gebe aber auch schon Forschung zu Riblets auf Turbinenschaufeln, die entweder als Beschichtung aufgetragen oder mittels hochpräziser Laserimpulse in die Schaufeloberfläche eingebracht werden.
Sollten die Nachfolgeprojekte von TURANDOT weiter erfolgreich verlaufen, vor allem hinsichtlich Temperaturbeständigkeit und Lebensdauer der Riblet-Oberflächen, könnte die Technologie in etwa drei Jahren marktreif sein.